Розрахунок показників сушильного агрегату на базі сушильної камери УЛ – 2
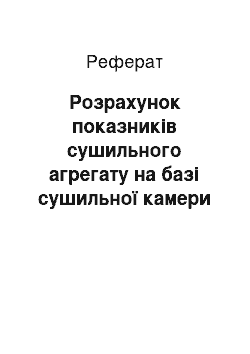
На ІІІ ступень режиму сушіння переходимо при досягненні п/м вологості 20%. При сушінні на ІІІ режимі, проводиться кінцева термовологообробка при досягненні матеріалом заданої кінцевої вологості. Температуру у камері підвищують на 8×02DAС вищою, ніж на останньому ступені режиму, психрометрична різниця дорівнює від 0,5 до 1×02DAС. Тривалість кінцевої термовологообробки визначаємо з табл.16 ст. 127… Читати ще >
Розрахунок показників сушильного агрегату на базі сушильної камери УЛ – 2 (реферат, курсова, диплом, контрольна)
Розрахункова робота.
на тему: «Розрахунок показників сушильного агрегату на базі сушильної камери УЛ — 2 «.
Зміст.
Вступ.
1.Вибір режимів сушіння.
1.1Розрахунок тепловологообробки.
2. Розрахунок тривалості сушіння і обороту камер
3. Перерахунок об'єму фактичного пиломатеріалу в об'єм умовного матеріалу.
4. Розрахунок річної продуктивності камери в умовному матеріалі.
5. Розрахунок необхідної кількості сушильних камер.
6.Вибір розрахункового матеріалу.
7. Визначити параметри агента сушіння на вході і виході зі стосу.
8. Опис технологічного процесу сушіння.
8.1 Транспортування сирих пиломатеріалів в сушильний цех.
8.2 Формування штабелів для сушіння.
8.3 Транспортування сушильних штабелів в середині цеху.
8.4 Опис конструкції камери.
8.5 Пуск і завантаження камери.
8.6 Технологічні етапи сушіння пиломатеріалів.
8.7 Контроль і регулювання параметрів агента сушіння.
8.8 Контроль вологості деревини в процесі сушіння.
8.9 Показники якості сушіння.
8.10 Розформування висушених штабелів.
9.Техніко-економічні показники.
Вступ.
Одним із факторів підвищення якості пиломатеріалів є їх сушіння (видалення вологи із різних шарів деревини шляхом випаровування).Це обов’язковий етап технологічного процесу лісопильного і деревообробного виробництва. Воно являється енергомістким процесом, пов’язаним з значними витратами палива, пари, а також електроенергії.В результаті сушіння деревина із природнього матеріалу перетворюються в промисловий матеріал, який відповідає різноманітним вимогам, котрі вимагаються від нього в різних виробничих і побутових умовах.
При зменшенні вологості деревини покращуються її фізико механічні і експлуатаційні властивості. Деревина, яка містить велику кількість вологи легко уражається грибами, в результаті чого вона загниває. Суха ж деревина відрізняється великою стійкістю до різних уражень. Зменшення вологості деревини приводить до зменшення її маси і одночасному підвищенню міцності. Суха деревина на відміну від вологої легко піддається обробці. Таким чином, сушіння проводять з метою: попередження деформації деталей; запобігання від псування; збільшення міцності і підвищення якості обробки.
В галузі сушіння деревини за останні роки досягнуто певних успіхів: збільшилась потужність камерного сушіння за рахунок введення в експлуатацію нової вітчизняної і зарубіжної техніки; організовано серійне виробництво збірно-металевих камер періодичної діїї; на лісопильно-деревообробних підприємствах майже в два рази зменшилась кількість низькопродуктивних камер старих типів, збільшився рівень механізації навантажувально-розвантажувальних і транспортних робіт; запроваджені нові лінії сушіння з підвищеною висотою штабелів.
Одночасно із збільшенням потужностей камерного сушіння пиломатеріалів на лісопильних підприємствах значно підвищились вимоги до якості висушеного матеріалу, розробляються і вводяться нові оптимальні режими сушіння. Їх впровадження дало можливість більш чітко керувати процесом сушіння і забезпечити високу якість висушеного матеріалу. Також слід відмітити такий факт, що промислове сушіння деревини відноситься до галузі виробництва, технологічний процес якої практично не впливає на забруднення навколишнього середовища.
Поряд з досягнутими успіхами в галузі сушіння все ще є недоліки і не вирішені питання. Об'єм сушіння не в повній мірі задовільняє потреби в сухих пиломатеріалах. Якість сушіння пиломатеріалів на деяких підприємствах знаходиться на невисокому рівні, спостерігається покороблення деревини, перехід із високих в більш низькі сорти, нерівномірність просихання пиломатеріалів по об'єму штабеля. Це зумовлене не дотриманням всіх норм і параметрів процесу сушіння.
Але незважаючи на ці недоліки сушіння все одно є невід'ємною операцією в переважній більшості технологічних процесів деревообробки.
1.Вибір режимів сушіння Залежно від вимог, які ставлять до якості висушених пиломатеріалів, вони можуть висушуватися режимами різних категорій за температурним рівнем: м’якими (М), нормальними (Н), форсованими (Ф) і високотемепературними (ВТ).
При сушінні до транспортної вологості за 0 категорією якості сушіння використовують м’які режими сушіння. При сушінні до експлуаційної вологості за І категорією використовують нормальні режими, а у випадках, коли ставлять осбливо високі вимоги до якості деревини-м'які режими. При сушінні до експлуатаційної вологості за ІІ і ІІІ категоріями якості можуть використовуватися нормальні, форсовані і високотемпературні режими.
С.
В кожному конктерному випадку тієї чи іншої категорії вибирають з врахуванням їх впливу на властивості деревини.
М’які режими — забезпечують бездефектне сушіння п/м при повному збереженні природніх фізико — механічних властивостей та кольору. Вони рекомендуються для експортних матеріалів (W — 19%), а також для пиломатеріалів вищих сортів. Це 0 та 1 категорія якості сушіння.
Нормальні режими — забезпечують бездефектне сушіння п/м при повному збереженні міцності деревини та незначній зміні кольору. Це друга категорія якості сушіння, тобто меблеві заготовки, столярно — будівельні вироби, деталі вагоно та автобудування.
Форсовані режими — забезпечують бездефектне сушіння п/м з незначним зменшенням міцності деревини на статичний згин, розтяг та стиск, з можливим потемнінням. Це третя категорія якості сушіння.
Високотемпературні режими — забезпечують сушіння п/м при незначній зміні міцності на статичний згин, розтяг та стиск, але при значному зменшенні міцності до 35%.
Режим сушіння вибирають за певною таблицею, а саме 3.3.1 ст.51(Г) томущо задано п/м хвойний, категорія якості сушіння 2, режим сушіння Н, камера УЛ — 2 періодичної дії.
Режим сушіння для кедра.
W п/м >35% 64 3 0.86.
W п/м 35 — 25% 68 7 0.71.
W п/м < 25% 85 24 0.33.
Режим сушіння для липи товщиною 35 мм вибираємо за певною таблицею, а саме 3.3.3 ст. 51 (Г) томущо задано п/м листяне категорія якості сушіння 2, режим сушіння Н, камера УЛ — 2 періодичної дії.
W п/м >35% 69 4 0.84.
W п/м 35 — 25% 73 7 0.72.
W п/м < 25% 91 25 0.34.
Режим сушіння для вільхи товщиною 28 мм вибираємо за певною таблицею, а саме 3.3.3 ст. 51 (Г) томущо задано п/м листяне категорія якості сушіння 2, режим сушіння Н, камера УЛ — 2 періодичної дії.
W п/м >35% 69 6 0.76.
W п/м 35 — 25% 73 10 0.63.
W п/м < 25% 91 28 0.30.
Розрахунок тепловологообробки.
В цілому камерне сушіння пиломатеріалів складається з ряду технологічних і контрольних операцій, які виконують в певній послідовності.
До технологічних операцій процесу сушіння відносять початковий прогрів, саме сушіння по визначеному режимі, кінцева вологотеплообробка, додаткова, проміжна і кондеціонування.
Початковий прогрів деревини проводиться після завантаження в камеру матеріалу з метою швидкого нагрівання деревини. Для цього деревину визначений час витримують у повітрі підвищеної температури і високої степені насичення або в чистому, насиченому парою.
При прогріві пиломатеріалів шпилькових порід крім модрини температура вибирається по Табл.15 (ст. 125 Расєв, 90).При прогріві пиломатеріалів модрини температура повинна бути вища на 5×02DAС ніж у першій ступені режиму сушіння.
Тривалість вибирають t<0×02DAС-1,5…2 год. на кожен сантиметр товщини для шпилькових порід.
Проміжкова вологотеплообробка провидиться для пиломатеріалів великої товщини. Для цього температуру підвищуємо на 8×02DAС, перед переходом натретю ступінь режиму сушіння.Тривалість визначають за Табл.16(ст. 127 Расєв, 90) у відношенні 1/3 від загальної тривалості.
Кінцеву вологотеплообробку проводять при досягненні матеріалом заданої кінцевої вологості при підвищеній температурі і вологості.Мета такої операції-зняти остаточні деформації і напруження в матеріалі.Тому температуру в камері підвищують на 8×02DAС вище третьої ступені режиму сушіння, але не більше 100×02DAС.Тривалість кінцевої вологотеплообробки вибираємо з Табл.16(ст. 127 Расєв, 90), 2/3 від загальної тривалості.
Вибираємо режим та тривалість початкового прогріву для кедра.
С (беремо з таблиці 15 Расев).
С.
— для літніх умов 1,5 год. на кожен сантиметр прогріву = 9год.
Вибираємо режим та тривалість проміжкової тепловологообробки.
С.
С.
3 год.
Вибираємо режим та тривалість кінцевої тепловологообробки.
С.
С.
6 год.
Вибираємо режим та тривалість початкового прогріву для липи.
С.
С.
літніх умов 1,5 год. на кожен сантиметр прогріву =3 год.
Вибираємо режим та тривалість проміжкової тепловологообробки.
С.
С.
— 2,3 год.
Вибираємо режим та тривалість кінцевої тепловологообробки.
С.
С.
— 1,3 год.
Вибираємо режим та тривалість початкового прогріву для вільхи.
С.
С.
— 3 год.
Вибираємо режим та тривалість проміжкової тепловологообробки.
С.
С.
— 2,3 год Вибираємо режим та тривалість кінцевої тепловологообробки.
С.
С.
— 1,3 год.
2. Розрахунок тривалості сушіння і обороту камер
Загальна тривалість сушіння фактичного і умовного матеріалу з урахуванням початкового прогрівання і термовологообробки визначають за формулою:
x03C4суш.= x03C4вих.· Ар·Ац·Ав·Ая·Ад, год.
де:x03C4вихвихідна тривалість власне сушіння п/м заданої породи і розмірів нормальним режимом від початкової вологості Wп=60% до кінцевої Wк=12% у камерах з реверсивною циркуляцією середньої інтенсивності, год.(Гербей ст. 32 таб.2.1.1).
АрАцАвАя Адпоправочні коефіцієнти, які враховують: Ар-категорію режиму сушіння (Гербей ст.33);Ацінтенсивність циркуляції.(Гербей ст. 34 таб.2.1.2);Авпочаткову і кінцеву вологість (Гербей ст. 34 таб.2.1.3);Аяякість сушіння (Гербей ст.35) ;Ад-довжину матеріалу (Гербей ст. 34 таб.2.1.4).
Значення коефіцієнтів знаходять за таблицями.
Швидкість циркуляції а/с по матеріалу в штабелі необхідно брати для камери УЛ-2×03C9шт.=1,5…3м/с.
Для кедра.
=125 год.
Ар = 1.
Ац = 0,84.
Ав = 0,78.
Ак = 1,05.
Ад = 1.
3,5 доби.
Для липи.
=94 год.
Ар = 1.
Ац = 0,79.
Ав = 1,11.
Ак = 1,15.
Ад = 1.
3,9 доби.
Для вільхи.
=85 год.
Ар = 1.
Ац = 0,56.
Ав = 1,27.
Ак = 1,15.
Ад = 1.
2,6 доби.
Умовний матеріал.
=88 год.
Ар = 1.
Ац = 0,75.
Ав = 1.
Ак = 1,15.
Ад = 0,93.
2,9 доби.
Розрахунок тривалості сушння і обороту камери Таблиця 2.
Характеристика п/м Категорія якості Категорія режиму сушіння Тривалість сушіння, x03C4вих, год. Коефіцієнти x03C4суш. x03C4об. діб.
Порода Товщина, мм Ширина, мм Вологість,%.
Ар Ац Ав Ая Ад год. діб.
Wп Wк.
1 2 3 4 5 6 7 8 9 10 11 12 13 14 15 16.
Кедр 60 150 70 10 ІІ Н 125 1 0,84 0,78 1,05 1 86 3,5.
Липа 35 150 60 10 ІІ Н 94 1 0,79 1,11 1,15 1 95 3,9.
Вільха 28 150 70 9 ІІ Н 85 1 0,56 1,027 1,15 1 65,4 2,6.
3. Перерахунок об'єму фактичного пиломатеріалу в об'єм умовного матеріалу.
) за формулою :
).
).
— коефіцієнт об'ємного заповнення матеріалу (таб. 2.4.2).
— - коефіцієнт об'ємного заповнення для фактичного матеріалу однакової характеристики .
— тривалість одного оберту камери для умовного матеріалу.
— тривалість одного оберту камери для фактичного матеріалу однакової характеристики.
Перерахунок об'ємного матеріалу в матеріал фактичний для кедра здійснюється за формулою:
= коефіцієнт умовного заповнення матеріалу беремо з таблиці 2.4.2 (Г ст. 44) = 0,438.
= беремо з таблиці 2.4.2 (Г ст. 44) = 0,502.
2,9 + 0,1 = 3 доби.
3,5 + 0,1 = 3,6 доби.
/рік.
Перерахунок об'ємного матеріалу в матеріал фактичний для липи здійснюється за формулою:
= коефіцієнт умовного заповнення матеріалу беремо з таблиці 2.4.2 (Г ст. 44) = 0,438.
= беремо з таблиці 2.4.2 (Г ст. 44) = 0,399.
2,9 + 0,1 = 3 доби.
3,9 + 0,1 = 4 доби.
/рік.
Перерахунок об'ємного матеріалу в матеріал фактичний для вільхи здійснюється за формулою:
= коефіцієнт умовного заповнення матеріалу беремо з таблиці 2.4.2 (Г ст. 44) = 0,438.
= беремо з таблиці 2.4.2 (Г ст. 44) = 0,356.
2,9 + 0,1 = 3 доби.
2,6 + 0,1 = 2,7 доби.
/рік.
Таблиця 3.
Заданий формат В умовному матеріалі.
1 2 3 4 5 6 7 8 9.
Кедр 60 150 3,6 3 0,502 0,438 4000.
Липа 35 150 4 3 0,399 0,438 4000.
Вільха 28 150 2,7 3 0,356 0,438 4000.
4. Розрахунок річної продуктивності камери в умовному матеріалі.
Продуктивність сушильного матеріалу розраховується на певний період (місяць, квартал, рік). Продуктивність сушильної камери в умовному матеріалі розраховується для того щоб спланувати роботу сушильної камери на наступний рік. За умовний матеріал прийнято обрізні дошки товщиною 40 мм, шириною 150 мм довжиною більше 1 метра, порода сосна, які висушуються по ІІ категорії якості сушіння від початкової вологості 60% до кінцевої 12%.
Розрахунок річної продуктивності камери в умовному матеріалі розраховується за формулою :
2,9 + 0,1 = 3 доби.
335 — це плановий робочий час сушильної камери в добах.
С = 335/365 = 0,92.
яку завантажують в камеру або це ємність сушильної камери.
l — довжина камери.
b — ширина камери.
h — висота камери.
m — кількість стосів в даній сушильній камері.
= 3.
l =0,92.
b = 6,5.
h = 2,6.
m = 2.
= 0,438.
/р
5. Розрахунок необхідної кількості сушильних камер.
При складанні виробничого плану сушильного цеху визначають специфікацію і об'єм висушеного матеріалу в рік, виходячи з плану випуску готової продукції чи замовлень. Об'єм п/м заданої специфікації перераховують в умовний матеріал, потім визначають планову продуктивність сушильної камери заданої марки в рік. Кількість сушильних камер для виконання заданої специфікації і річної програми визначають за формулою :
n — кількість камер (шт.).
— загальна кількість умовного матеріалу.
— продуктивність однієї камери для умовного матеріалу.
Розрахунок необхідної кількості сушильних камер для кедра:
шт.
Розрахунок необхідної кількості сушильних камер для липи:
шт.
Розрахунок необхідної кількості сушильних камер для вільхи:
шт.
6.Вибір розрахункового матеріалу.
При проектуванні лісосушильних камер за розрахунковий матеріал беруть як правило соснові обрізні дошки товщиною 25 мм, шириною не менше 180 мм, початкова вологість 80%, кінцева залежить від призначення матеріалу. Якщо в завданні на проектування немає таких дощок то за розрахунковий матеріал беруть той який найшвидше висихає з зазадої специфікації. В цьому випадку камери забезпечують сушіння будьякого матеріалу з заданої специфікації. В даному випадку за розрахунковий матеріал приймаємо вільху товщиною 28 мм, товщиною 150 мм, довжиною 3 метри.
7. Визначити параметри агента сушіння на вході і виході зі стосу.
).
кг/м3.
де: x03C1 ум — умовна густина розрахункового матеріалу (табл.Д.21).
Wп, Wк — початкова і кінцева вологість розрахункового матеріалу (завдання К.П.).
7.2 Маса вологи, що випаровується за час одного камерообороту:
· Е= 256,2*21,7=5559,5кг/об Де: Е-місткість камери, м3.
Е=Г· x03B2ф=60,8*0,356=21,7 м³.
Де :Г-габаритний об'єм всіх штабелів у камері, м3.
x03B2фкоефіцієнт об'ємного заповнення штабелю фактичним (розрахунковим) матеріалом.
Значення Г і x03B2ф визначені в технологічному розрахунку .
7.3 Маса вологи, що випаровується з камери за секунду:
кг де: x03C4вл. суштривалість власне сушіння розрахункового матеріалу без врахування тривалості початкового прогрівання і термовологообробок:
год.
де :x03C4сушзагальна тривалість сушіння розрахункового матеріалу, год.
Аккоефіцієнт, який враховує якість сушіння, його значення було визначено в технологічному розрахунку.
7.4 Розрахункова кількість випаровуваної вологи за секунду:
Мр=Мс· Х=0,028*1,2=0,034.
Де :Хкоефіцієнт нерівномірності швидкості сушіння (Х=1,2) для камер періодичної дії при сушінні повітрям до Wк=12−15%.
7.5Розрахунок об'єму циркулюючого агента сушіння і його параметрів на виході зі штабелю.
7.5.1 Об'єм циркулюючого по матеріалу агента сушіння:
Vц=x03C9шт· Fж.п.шт = 2,5*11,7=29,3.
де: шт. — розрахункова швидкість циркуляції а/с через штабель, м/с (з технічної характеристики камери).
Fж .п.штживий перетин штабелю, м2.
Fж. п. шт=n· l·h (1-x03B2в·x03B2д)=6,5*1,8*2,6(1−1*0,615) = 11,7 м².
Де :nкількість штабелів в площині, перпендикулярній до напряму циркуляції а/с.
l, h-довжина і висота штабелю, м.
x03B2вкоефіцієнт заповнення штабелю по висоті (Гербей ст.45).
x03B2дкоефіцієнт заповнення штабелю по довжині (Гербей ст.44).
7.6 Маса по матеріалу агента сушіння за секунду:
кг де: V1-питомий об'єм а/с на розрахунковому ступені режиму.
7.7 Питома витрата циркулюючого агента сушіння на 1 кг випаровуваної вологи:
кг/кл. вол.
2.4.4 Вологовміст агента сушіння на виході зі штабелю:
г/кг.
Інші параметри а/с на виході зі штабелю визначають за допомогою побудови ліній процесу сушіння на Іdдіаграмі.Точку 1, яка характеризує стан а/с на вході в штабель знаходимо за t1, x03C61. Точку 2, яка характеризує параметри а/с на виході зі штабелю знаходимо на перетині лінії I=const (I1=I2), яка виходить з точки 1 з лінією d2=const.
Праметри а/с на виході зі штабелю заносимо в Таблицю.
Параметри агента сушіння на виході зі штабелю Таблиця 4.
1 кг/м3 0.93.
Питомий об'єм V1 м3/кг 1.25.
8. Опис технологічного процесу сушіння.
8.1 Транспортування сирих пиломатеріалів в сушильний цех.
Сирі пиломатеріали привозять зі складу сировини у вигляді суцільних пакетів, які транспортуються до сушильного цеху автопогрузчиком.
8.2 Формування штабелів для сушіння.
При камерному сушінні використовуємо штабель суцільного типу, розміри якого 6,5×1,8×2,6 м, який формують за допомогою ліфта Л-6,5−15.
Штабель п/м необхідно викладати правильної геометричної форми-у вигляді паралелепіпеда. Бокові і торцеві поверхні повинні бути строго вертикальні. В один штабель укладають дошки тільки однієї породи і одної товщини. По вологості п/м, які завантажуються слід сортувати на сирі і повітряно-сухі, не змішуючи їх в один штабель. Необрізні дошки укладаються комлями в різні сторони.
Основа штабеля повинна бути строго горизонтальна і досить жорстка. Як підштабельні основи використовують трекові вагонетки, які складаються з трьох пар треків і зв’язані підштабельними брусами.
При укладанні штабелів слід користуватися габаритними штабельними шаблонами.
Також при формуванні штабеля застосовують прокладки. Вони мають товщину 25 мм і ширину 40…50мм, повинні бути строго прокалібровані і висушені. Їх необхідно укладати строго вертикально, одну під другу.
8.3 Транспортування сушильних штабелів в середині цеху.
Для внутрішньоцехових перевезень сформованих сушильних штабелів використовуємо рейкову колію шириною 1000 мм і траверсні візки марки ЭТ-6,5 М.
Стан рейкової колії систематично контролюється, не допускається непрямолінійність рейок, нестабільна ширина колії, незбігання рівня рейок на траверсному візку і рейок, які впираються в траверсний коридор.
Механізація переміщення штабелів здійснюється за допомогою трособлокової системи і тягової лебідки, яка встановлена на траверсних візках.
8.4 Опис конструкції камери .
В камері УЛ-2 а/с є пароповітряна суміш яка циркулює в поперечно-вертикальному напрямі. Камера працює в такій послідовності: а/с рухається в поперек камери, проходячи послідовно через труби калорифера і штабелі. При циркуляції по годинниковій стрілці в лівій частині вентиляційного каналу утворюється розрідження, а в правій-підвищенний тиск.
В даному випадку лівий розпридільний вентиляційний канал служить для притоку свіжого, а правий-для виділення відпрацьованого повітря. Призначення каналів міняється при реверсивній циркуляції.
Камера є збірнометалева вмісткість в два нормальні штабелі які монтуються на підготовленному фундаменті з таких частин: з передньої, з задньої, чотирьох боквих пенелей і двох верхніх секцій.
В верхній секції змонтовано шість осьових ревресивних вентилятори, пластинчасті калорифери і зволожуючі труби. Камери можуть працювати як при високотемпературному процесі на перегрітому парі, так і при низькотемпературному на пароповітряній суміші.
При роботі на пароповітряній суміші приток свіжого і виділення відпрацьованого повітря здійснюється через вентиляційні канали.
При роботі на перегрітій парі вентиляційні канали закриті, а вода, випарувана з деревини, виділяється у вигляді пари через гідравлічний затвор.
Завдяки реверсивним вентиляторам здійснюється реверсивна циркуляція, що значно покращує сушіння п/м.
8.5 Пуск і завантаження камери .
Перед завантаженням штабелів камеру необхідно прогріти, щоб не допускати конденсації вологи на огородженні камери і обладнанні. Якщо камера не вистигла після вивантаження, пару в калорифер необхідно впускати за 10…30хв до завантаження матеріалу. В момент впуску пари відкривають на 10…15хв вентиль на обдувній трубі конденсатовідівдника. Пару впускають в калорифер поступово, відкриваючи вентиль. Після продувки калорифера вентиль на обдувній трубі конденсатовідвідника закривають, і система починає працювати нормальночерез кондесатовідвідник.
У пусковий період припливно-витяжні канали мають бути закриті. Сформований штабель завантажують у камеру. Недопускається завантаження в камеру неповногабаритного штабеля.
8.6 Технологічні етапи сушіння пиломатеріалів.
Першою технологічною операцією після завантаження камери є початкове прогрівання деревини. Для інтенсивного початкового прогрівання перед сушінням в камері створюється висока відносна вологість а/с при підвищеній температурі. Температуру середовища при прогріванні п/м листяних порід підтримують на 8×02DAС більше від першого ступеня режиму сушки. Для розрахункового матеріалу (табл.15 ст. 125 Расєв 90) буде становити 85×02DAС при психрометричній різниці від 0,5 до 1×02DAС і степенню насичення 0,99. Орієнтовну тривалість початкового прогріву визначають для зимових умов з розрахунку 2 год. на кожний сантиметр товщини, тобто 9 год. Всі інші матеріали заданої специфікації див. Таблицю 2 К.П. В період прогрівання до камери подають пару через зволожуючі труби при ввімкнених калориферах, працюючих вентиляторах і закритих припливно-витяжних каналах.
Після висушування п/м до вологості 30% переходимо на ІІ ступінь режиму сушіння, на якій проводиться проміжкова термовологообробка для п/м підвищеної товщини, для якої температура підвищується на 8×02DAС, психрометрична різниця підвищується від 1,5 до 2×02DAС, а степінь насичення 0,96. Тривалість проміжної термовологообробки визначаємо за табл.16 ст. 127 Расєв 90 — 1/3 від загальної тривалості. Для розрахункового матеріалу проміжкова термовологообробка не проводиться, для інших п/м, які піддаються проміжній термовологообробці див. Таблиця 2 К.П.
На ІІІ ступень режиму сушіння переходимо при досягненні п/м вологості 20%. При сушінні на ІІІ режимі, проводиться кінцева термовологообробка при досягненні матеріалом заданої кінцевої вологості. Температуру у камері підвищують на 8×02DAС вищою, ніж на останньому ступені режиму, психрометрична різниця дорівнює від 0,5 до 1×02DAС. Тривалість кінцевої термовологообробки визначаємо з табл.16 ст. 127 Расєв 90 — 2/3 від загальної тривалості. Для розрахункового матеріалу параметри будуть такими: температура 100×02DAС, психрометрична різниця 0,5×02DAС, степінь насичення 0,99 і тривалість 6 год. Параметри сушіння для п/м заданої специфікації див. Таблицю 2 К.П.
Після закінчення кінцевої термовологообробки закривають зволожуючі труби, в камері створюють параметри а/с по останньому ступені режиму на протязі 2,5 год. проводять підсушування верхніх шарів. Потім із штабеля вибирають проби для визначення показників якості сушіння.
Якщо деревина відповідає заданим вимогам, подача пари в калорифери припиняється, камеру охолоджують до 30…40×02DAС, спочатку при відкритих припливно-витяжних каналах, а потім при напіввідкритих дверях. Потім штабель викочують із камери. Тривалість охолодження розрахункового матеріалу 4,5год.
8.7 Контроль і регулювання параметрів агента сушіння.
За станом а/с в камері спостерігають щогодини, покази психрометра записують в журнал. Завданням регулювання параметрів а/с є підтримка їх на заданому рівні. Температура регулюється впуском кількості пари, яка надходить до калорифера. Регулювання вологості здійснюється шляхом відкривання або закривання припливно-витяжних каналів, а також пуском пари безпосередньо до камери. Регулювання параметрів а/с може бути ручним і автоматичним.
Для визначення температури застосовуємо ртутні склянні технічні термометри ТТ-3Б. Для визначення психрометричної різниці використовуємо стаціонарні недистанційні психрометри. Для визначення швидкості а/с служить крильчатий анемометр, а для визначення тиску — манометр з одновитковою трубчатою пружиною.
8.8 Контроль вологості деревини в процесі сушіння.
Для встановлення моменту переходу з одного ступеня режиму сушіння на другий і закінчення процесу сушіння, необхідно знати вологість висушуваних п/м. В даний час основним методом для визначення вологості п/м є ваговий. Він оснований на зважуванні і висушуванні зразків, які відбираються з партії деревних сортиментів, що контролюються. Від дошки або заготовки на відстані 300…500мм від торця випилюють поперечним зрізом пробу розміром вздовж волокон біля 10 мм. Ця проба називається секцією вологості. Її старанно зачищують від завусин, після чого негайно зважують на технічній вазі з похибкою до 0,1 г. Одержане значення початкової маси реєструють в спеціальному журналі.
Потім секцію розташовують в сушильній шафі і сушать. Періодично її виймають з шафи і зважують, відмічаючи кожен раз в журналі результати зважування. Перше зважування проводять через 6 год. а наступні через кожні 2 год. Секцію витримують в сушильній шафі до тих пір поки її маса не перестане змінюватись. Постійну масу приймають рівною її масі в абсолютно сухому стані. Вологість розраховують по відношенню:
W=[(mн-mсух)/mсух]· 100.
Для визначення вологості одної дошки або заготовки необхідно випилювати із неї не менше двох секцій. Число контрольних дошок залежить від величини контролюючої партії, а також потрібної точності і надійності контролю.
8.9 Показники якості сушіння.
Норми показників якості сушіння п/м і заготовок встановлені залежно від категорії якості сушіння. До них відносять:
відповідність середньої вологості висушених п/м у штабелі заданій кінцевій вологості -10%.
відхилення вологості окремих дощок або заготовок від середньої вологості п/м у штабелі -+3%.
перепад вологості за товщиною матеріалу -3,5%.
залишкові напруження у висушених п/м — не більше 2%.
8.10 Розформування висушених штабелів.
Розформування сушильних штабелів проводиться не відразу після вивантаження їх з камери, а після відповідної витримки в охолоджувальному приміщенні, тривалість витримки беруть приблизно 24год для тонкого п/м і 36…48год для товстого.
Для розформування суцільних штабелів, як і для формування застосовується ліфт Л-6,5−15.
Зберігання висушених пиломатеріалів.
Пиломатеріали можуть бути висушені до транспортної і експлуатаційної вологості. В нашому випадку п/м висушені до експлуатаційної вологості. Вони повинні зберігатися в закритих опалювальних приміщеннях (складах) при плюсовій температурі повітря і відповідних значеннях відносної вологості, значення якої залежить від категорії якості сушіння, кінцевої вологості деревини і терміну зберігання.Допустиме зберігання п/м на відкритому складі. Якщо пакети захищені вологонепроникною упаковкою або в закритих неопалювальних складах протягом обмеженого терміну.
9.Техніко-економічні показники Техніко-економічні показники Таблиця 5.
№ п/п Показники Одиниці виміру Значення Примітка.
15 Тип камери Габаритні розміри штабеля Довжина Ширина Висота Число штабелів.
Ємкість камери в умовному матеріалі.
Ємкість камери в фактичному матеріалі.
Річна продуктивність сушильної камери в умовному матеріалі.
Внутрішні розміри сушильної камери Довжина Ширина Висота Агент сушіння Кількість вентиляторів Характеристика вентилятора Продуктивність Тиск Характеристика електродвигуна для приводу вентилятора Потужність Число обертів Кількість двигунів Швидкість руху а/с через штабель Характеристика теплового обладнання Тип калорифера Кількість калориферів Поверхня нагріву Максимальна витрата пари на сушіння Кількість сушильних камер в цеху.
м м.
м шт м3.
м3.
м3/рік м.
м м.
пароповітряна суміш шт м3/с Па кВт об/хв шт м/с пластинчастий шт м2.
т/рік шт УЛ-2.
6,5.
1,8.
2,6.
13,8.
4,4.
У12 № 10.
12,082.
945,724.
4A200М2Y3.
34,987.
2,5.
КФБ-11.
8283,45.