Технология виготовлення розподільного вала
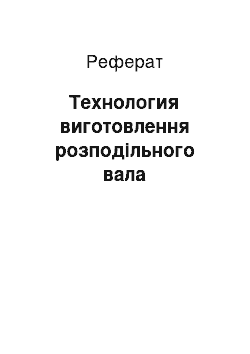
Гомогенізація. Дифузний відпал застосовують для зливків легованої почав із метою зменшення дендритной чи внутрикристаллической ликвации, яка підвищує схильність стали, оброблюваної тиском, до тендітному руйнації, до анизотропии властивостей й виникнення таких дефектів, як шиферность і флокены. Оющая тривалість диффузионного отжига (нагрівання, витримка та повільний охолодження) великих садок… Читати ще >
Технология виготовлення розподільного вала (реферат, курсова, диплом, контрольна)
Реферат.
25 з., 6 табл., библ., 5 наим. Термообробка, перліт, феррит, гарт, відпустку, нормалізація, хімічний склад, легирующие елементи, цементация.
Данная робота присвячена обгрунтуванню потребу використання стали, зазначеної на кресленні, й розробка пропозицій з можливості її заміни при изгатовлении розподільного валу. Діяльність спочатку аналізуються умови експлуатації розподільного валу, з’ясовуються вимоги, предьявляемые щодо нього. По полученым даним обгрунтовується використання стали, зазначеної на кресленні, предлогается її замінник розробляють режим термічної обробки, який би необхідний рівень механічних властивостей металла.
Реферат Введение.
1. Аналіз умов праці детали.
2. Обгрунтування застосування використовуваної сталі та пропозиції щодо її заміні для конкретної детали.
3. Розробка режимів по термічної обработке.
4. Поверхове зміцнення, захисне покрытие.
5. Розробка технології виготовлення детали.
6. Можливі причини шлюбу термічної обработки.
7. Заходи з техніці безпеки при термічної обработке Заключение Список використовуваної литературы.
Розподільний вал є однією з найважливіших елементів різних механізмів і машин. Він служить передачі обертаючого моменту. При розташуванні валу в голівці циліндрів привід здійснюється ланцюгової чи зубчато ремінної передачею, у блоці целиндров із засобів шестерён. Распред вал в зависимисти від області застосування виготовляється із різних матеріалів. Найбільш распространённый-сталь.
1. Аналіз умов праці детали.
В механічних передачах, різних вузлах машин утримуватися распред вали, призначені для потдерживания вращающих елементів машин. Валі є ланки механізму, передають крутящие моменти, і по повз вигину які відчувають крутіння. Распред вали є суттєвою частиною автомтических машин, парових і двигунів внутрішнього згоряння. Распред вал наводиться на дію з допомогою відповідної передачі. Распред вал на двигуні служить для приводу клапанів. Кулочки які з штовхачами клапанів, і навіть опорні шийки, ексцентрики й окремі торцевые опорні поверхні повинні обдадать високої изностойкостью.
Одне з варіантів виготовлення й зміцнення распред валу. Вали з цементируемых сталей упрочняемые цементацыей із наступною поверхневою загартованістю при поверхневому индукционном нагріванні кулачків і шийок. І тут облегчаеся обробка валу резаньем, але зростає загальна трудоёмкость і складність термо обробки. Распред вал при эксплуотации можент мати такі дефекты:
погнутось, тріщини, знос опорних шийок і кулачків профілем. Прогнутость валу устроняется правкою на пресі. Опорні шийки ремонтують шлифованием до ремонтних розмірів. Кулачки, зношені за висотою, шліфують на полировально шліфувальних верстатах. При значному уменьшени діаметра цилинрической частини кулочка, і навіть за наявності рисок і раковин, не удоляемых дрібно зернистим бруском, распред вал заменяют.
2. Обгрунтування застосування використовуваної сталі та пропозиції щодо заміні її для конкретної детали.
Сталь 20Х — коннструкционная, легированноя. Призначення — чопи, вали, шестерні, обойми, гільзи, диски, важелі та інших. тетали яких застосовуються вимоги високої поверхневою твердості при не високої прчности серцевини деталі. Таблиця 2.1 Температура критичних точек.
|Ас1 |Ас2 (Асм) |Аr3 (Аrсм) |Аr1 |Мн | |750 |825 |755 |665 |390 |.
Таблица 2.2 Щодо хімічного складу % (ГОСТ 4543−71).
|C |Si |Mn |Cr |P |P.S |Cu |Ni | |0.17−0.2|0.17−0.37 |0.5−0.8 |0.7−1.0 |0.035 |0.035 |0.3 |0.3 | |3 | | | | | | | |.
Механічні властивості проката Заготовка — пруток. Важливі термробраблткиЦементація — 920−950 надворі Гарт — 800 у маслі Відпустку — 190 надворі Перетин — 60 мм Умовний межа плинності щонайменше 390 Мпа Временное опір розриву (межа міцності при розтягненні) — не менш 640 Мпа Відносне удлиннение при розриві не менее13% Відносне звуження щонайменше 40% Ударне в’язкість, певна на зразку з концентраторами типу U (KCU) — щонайменше 49Джсм Твердість по бринелю трохи більше 250.
Таблица 2.3 Хутро. властивості (ГОСТ 8479−70).
|Термо-об|Сечение |КП |Gо2 |Gв |?5 |? |Kcu|НВ,| |работ-ка| | | | | | |Дж|не | | | | | | | | |див |бол| | | | | МПа | % | | | | | | | Так само | | |Закалка,|До 100 |275 |275 |530 |20 |40 |44 |156| |відпустку | | | | | | | |-19| | | | | | | | | |7 |.
Технологічні свойства.
Температура кування, початку 1260, кінця 750. Заготівлі перерізом до 200 мм розладнуються надворі, 201−700 піддаються низкотемпературному отжигу. Зварюється без обмежень (крім химико термічної обробки деталей) Способи зварюванняручна дуговая зварювання, контактна. Обробатывается резаньем — в гарячому стані при НВ 131 і Gв=450Мпа, Коб. ст=1,3, Котв. спл=1,7 Замінник — стали 15Х, 20ХН, 12ХН2, 18ХГТ Таблица 2.4 Механічні властивості за нормальної температури відпустки 200 С.
|Температура|Go2 |G1 |?r |? |кcu | |відпустки | | | | |Джсм | | | МПа | % | | |200 |Пруток діаметром 25 мм, зкалка 900, олію | | |650 |880 |18 |58 |118 |.
Таблиця 2.5 Межа витривалості при n=10.
| G1, МПа | Стан стали | | 412 |Цементация.закалка.низкий відпустку. | | |Gо, 2=790 МПа, Gв=930 МПа, hrc | | |57−63 |.
Таблиця 2.6 Ударне в’язкість kcu, Джсм.
| температура |стан | |+20 |-20 |-40 |-60 | | |280−286 |280−289 |277−287 |268−274 |Пруток | | | | | |діаметром | | | | | |115мм, закалка| | | | | |, відпустку |.
Леговані стали мають найкращими механічними властивостями після термічної обробки (гарту, відпустки). У виробах великих перетинів (діаметром понад 15−20 мм) механічні властивості легованих сталей вище, ніж вуглецевих. Особливо сильно підвищуються межа плинності, відносне звуження і ударна в’язкість. Це тим, що леговані стали мають меншою критичної швидкістю гарту, а, отже, кращої прокаливаемостью. Після термічної обробки вони мають більш дрібне збіжжя та більш дисперсні структури. Через більшої прокаливаемости і меншою критичної швидкості гарту легована сталь дає змогу виробляти загартування деталей менш різких охолоджувачах (олії, повітрі), що зменшує деформацію виробів і небезпека освіти тріщин. Для виготовлення розподільного валу потрібно вибирати сталь, яка має переліченими властивостями і деталь, яка виконується, повинна мати в’язку серцевину і тверду поверхню. Ця сталь 20Х задовольняє наведеним вимогам і тому адресований виготовлення даного розподільного вала.
3. Розробка режимів термічної обработки Основными видами термічної обробки, різна змінюють структуру і властивості сталі та котрі призначаються залежно від вимог, що висуваються до напівфабрикатах (отливкам, поковкам, прокату тощо.) і готовим виробам, є відпал, нормалізація, гарт і отпуск.
Відпал I роду Цей вид отжига залежно від температурні умови виконання усуває фізичну чи хімічну неоднорідність, створену попередніми обробками. Характерна риса цього отжига у тому, що усунення неоднорідності відбувається незалежно від цього, протікають у сплавах нині обробці фазові перетворення чи ні. Тому відпал I роду можна робити при високих температурах вище або нижчий від температур фазових превращений.
Гомогенізація. Дифузний відпал застосовують для зливків легованої почав із метою зменшення дендритной чи внутрикристаллической ликвации, яка підвищує схильність стали, оброблюваної тиском, до тендітному руйнації, до анизотропии властивостей й виникнення таких дефектів, як шиферность і флокены. Оющая тривалість диффузионного отжига (нагрівання, витримка та повільний охолодження) великих садок металу сягає 50−100 годин і більше. Тривалість витримки — 8−20 годин. Для видалення поверхневих дефектів зливки після отжига іноді піддають нагріванню при 670−680 З протягом 1−16 годин, що знижує твердість. Рекристаллизационный відпал — нагрівання холоднодеформированной підросли температури рекристалізації, витримка нині температурі з наступним охолодженням. Цей вид отжига застосовують і після холодної обробки тиском як і проміжну операцію зі зняттям наклепа між операціями холодного деформирования. температура отжига задля досягнення рекристалізації з усього обсягу та скорочення часу процесу перевищує температуру порога рекристалізації. Тривалість нагріву від 0.5 до 1.5 годин. Відпал для зняття залишкових напруг застосовують для виливків, зварних виробів, деталей після оюработки різанням та інших., яких у процесі попередніх технологічних операцій через нерівномірного охолодження, неоднорідною пластичної деформації тощо. виникли залишкові напруги. відпал сталевих виробів проводиться за нормальної температури 160−700 із наступним повільним охолодженням. Відпал зі зняттям зварних напруг проводиться при 650−700 С.
Відпал II роду Полягає в нагревестали до температури вище точки Ас3 чи Ас1, витримці і, зазвичай, повільному охолодженні, у результаті якого фазові перетворення призводять до досягненню практично рівноважного структурного стану. Після отжига углеродистой стали виходять структури: феррит і перліт в доэвтектоидных сталях, перліт в эфтектоидной стали, перліт і первинний цементит в доэфтектоидных сталях. Після отжига сталь має низькою твердістю і міцністю за високої пластичності. Фазовая перекристалізація, що відбувається при отжиге, змаліє збіжжя та усуває видмонштеттову та інші несприятливі структури стали. Відпал у промисловості здебільшого є підготовчої термічної обробкою. Отжигу піддають виливки, поковки, прокат. Знижуючи проюность і твердість, відпал покращує обробку різанням посередньо і высокоуглеродистой стали. Подрібнюючи зерно, знімаючи внутрішня напруга і зменшуючи структурну неоднорідність, він сприяє підвищенню пластичності і в’язкості. Іноді відпал є остаточною термічної обробкою. Розрізняють такі види отжига: повний, ізотермічний, неполный.
Нормализация Она залежить від нагріванні доэвтектоидной стали до температури, перевищує точку Ас3 на 50 З, а эвтектоидной підросли Аст на 50 З, нетривалої витримці для прогріву садки і завершення фазових перетворень і охолоджень надворі. Нормалізація викликає повну фазову перекрристаллизацию сталі та усуває грубозернисту структуру, отриману при лиття чи прокатці, куванню чи штампування. Прискорений охолодження надворі призводить до розпаду аустеніту за більш низьких температурах, що підвищує дисперсність ферритно-цементитной структури та збільшує кількість перліту. Це підвищує на 10−15% міцність і твердість нормализованной посередньо і высокоуглеродистой стали по порівнянню з отожженной. Нормалізація горячекатанной стали підвищує її опір тендітному руйнації, які характеризуються зниженням порога хладноломкости і підвищенням роботи розвитку тріщини. Призначення нормалізації різна залежно від складу стали. Для низьковуглецевих сталей нормалізацію застосовують замість отжига. При підвищенні твердості нормалізація забезпечує велику продуктивність при обробці різанням й одержанні вищої чистої поверхні. Для виливків з среднеуглеродистой стали нормалізацію чи нормалізацію з великим відпусткою застосовують замість гарту й високого відпустки. Механічні властивості при цьому трохи нижче, але вироби піддадуться меншою деформації проти одержуваної при загартуванню і можливість появи тріщин практично виключається. Нормалізацію з наступним високим відпусткою (600−650 З) часто використовують для виправлення структури легованих сталей замість повного отжига, так як продуктивність і трудомісткість цих двох операцій вище, аніж одну отжига. Для конкретної деталі (розподільного валу) нормалізація проходить при температурі 880 із наступним охолодженням на воздухе.
Закалка Закалка — це термічна обробка, залежить від нагріванні стали до температури вище критичної чи температури розчинення надлишкових фаз, витримці і наступному охолодженні зі швидкістю, перевищує критичну. Гарт перестав бути остаточної операцією термічної обробки. Щоб зменшити тендітність і напруги, викликані загартованістю, й одержати необхідні механічні властивості сталь після гарту обов’язково піддають відпустці. Інструментальну сталь переважно піддають загартуванню і відпустці для підвищення твердості, зносостійкості та міцності, а конструкционную сталь — підвищення міцності, твердості, підвищення досить високої пластичності і в’язкості, а низки сталей і високої зносостійкості. Доэвтектоидной стали нагрівають до температури на 30−50 З вище точки Ас3. У цьому випадку сталь із вихідною структурою перлит-феррит при нагріванні набуває аустенитную структуру, яка за наступному охолодженні зі швидкістю вище критичної перетворюється на мартенсит. Загартування від температур відповідних межкритическому інтервалу (Ас1-Ас3), не застосовуються. Заэвтектоидные стали під загартування нагрівають трохи вища Ас1. За такої нагріванні утворюється аустенит за збереження певної кількості вторинного цементита. Після охолодження структура стали складається з мартенситу і нерозчинних частинок карбідів, які мають високої твердістю. Інтервал коливання температур гарту більшості сталей невеликий (15−20 З). Багатьом сталей температура нагріву під загартування значно перевищує критичні точки Ас1 і Ас3 (150−200 З), що необхідне переведення гривень у твердий розчин спеціальних карбідів й отримання необхідної легированности аустеніту. Охолодження при загартуванню має забезпечити отримання структури мартенситу в межах заданого перерізу вироби й не викликати закалочных дефектів: тріщин, деформацій, короблений і високих растягивающих залишкових напруг у поверхневих шарах. Зазвичай для гарту використовують неклеящие рідини — воду, водні розчини солей і лугів, олії. Є різноманітні способи гарту: безупинної, переривчастої, східчастої, гарт з самоотпуском, изотермическая і світла закалка.
Закаливаемость і прокаливаемость стали Закаливаемость — це здатність стали підвищувати твердість внаслідок гарту. Закаливаемость стали визначається вмістом у стали вуглецю. Що в мартенсите вуглецю, тим вищі її твердість. Легирующие елементи надають щодо невеличке впливом геть закаливаемость. Прокаливаемость — це здатність почали отримувати загартований шар в мартенситной чи тросто-мартенситной структурою і високої твердістю на або ту глибину. Прокаливаемость визначається критичної швидкістю охолодження, яка від складу стали. Якщо справжня швидкість охолодження в серцевині вироби перевищуватиме критичну швидкість загартуй, то сталь отримає мартенситную структуру з усього перерізу і тих самим матиме наскрізну прокаливаемость. Якщо справжня швидкість охолодження в серцевині буде набагато меншою Vкрю, то виріб прокалится на деяку глибину й прокаливаемость буде неповної. За глибину загартованого шару умовно приймають відстань від поверхні до полумартенситной зони. Діаметр заготівлі, у якої після гарту у цій охлождающей середовищі утворюється полумартенситная структура, називають критичним диаметром.
Отпуск Отпуск залежить від нагріванні загартованою стали до температури нижче Ас1, витримці при заданої певній температурі й наступному охолодженні з певною швидкістю. Відпустку є остаточною операцією термічної обробки, в результаті якої сталь отримує необхідні механічні властивості. Крім того, відпустку в цілому або частково усуває внутрішні напруги, які під час загартуванню. Ці напруги знімаються тим повнішим, що стоїть температура відпустки. Швидкість охолодження по відпустці також надає великий вплив на величину залишкових напруг. Чим повільніше охолодження, тим менше залишкове напруга. Бистре охолодження від 600 З відкриває нові теплові напруги. Через це вироби складної форми воизбежание їх коробления по відпустці при високих температур слід охолоджувати повільно, а вироби з легованих сталей, схильних до оборотного відпускної тендітності по відпустці при 500−600 З завжди слід охолоджувати швидко. Розрізняють низькотемпературний, среднетемпературный і високотемпературний відпустку. Низький відпустку проводять із нагріванням до 150−200 З, рідше до 240−250 З. у своїй знижуються внутрішні напруги, мартенсит гарту проводиться в відпущений мартенсит, підвищується міцність і трохи поліпшується в’язкість без помітного зниження твердості. Загартована сталь (0.5−1.3% З) після низького відпустки зберігає твердість не більше HRC 58−63, отже, високу зносостійкість. Але такий виріб не витримує значних динамічних навантажень. Низкотемпературному відпустці піддають тому ріжучий і вимірювальний інструмент з вуглецевих і низьколегованих сталей, і навіть датели, претерпевшие поверхневу загартування, цементацию, цианирование чи нитроцементацию. Тривалість відпустки зазвичай 1−2.5 години, а великих перетинів і вимірювальних інструментів призначають довший відпустку. Среднетемпературный відпустку виконують при 350−500 З повагою та застосовують головним чином заради пружин і ресор, і навіть для штампів. Така відпустка забезпечує високий межа пружності, межа витривалості і реакційну стійкість. Структура стали (0.45−0.8% З) після середнього відпустки — троостит відпустки чи троостомартенсит з твердістю HRC 40−50. Температуру відпустки треба обирати в такий спосіб, ніж викликати необоротною відпускної зрупкости. Охолодження по відпустці при 400−500 З слід здійснювати воді, що сприяє освіті лежить на поверхні стискають залишкових напруг, які збільшують межа витривалості пружин. Високотемпературний відпустку. Його проводять при 500−680 З. структура стали при високого відпустки — сорбит отпуска. высокий відпустку створює найкраще співвідношення міці й в’язкості стали. Його проводять із метою: 1. Зниження внутрішнього напруги; 2. Зниження твердості для обдирки зливка. Гарт з великим відпусткою з порівнянню з нормализованным чи отожженным станом одночасно підвищує пределя міці й текучемти, відносне звуження і особливо ударну в’язкість. Термічну обробку, що складається з гарту й високого відпустки, називають поліпшенням. Відпустку при 550−600 З протягом 1−2 годин майже зовсім знімає залишкове напруга, що виник при загартуванню. Частіше тривалість високого відпустки становить 1−6 годин залежно від габаритних розмірів виробів. Для конкретної деталі (розподільний вал) режими термічної обробки складаються з: Попередньої термічної обробки зливка, що складається із високого відпустки, після чого виробляється нормалізація. Далі проводиться правка деталі, які ліквідують різні спотворення розмірів. Далі проводять цементацию, що полягає у процесі насичення поверхневого шару стали вуглецем. Цементація й наступна термічна обробка одночасно підвищують межа витривалості. Тому після цементації проводиться остаточна термічна обробка, яка залежить від високому відпустці, загартуванню і низькому отпуске.
4. Поверхове упрочнение.
Газова цементація. Цей процес відбувається здійснюють нагріванням вироби серед газів, містять вуглець. Газова цементація має низку переваг по порівнянню з цементацией в твердому карбюрезаторе, тому її нині застосовують на заводах, виготовляють деталі масовими партіями. Що стосується газової цеменации можна було одержати задану концентрацію вуглецю в шарі; скорочується тривалість процесу, оскільки зайвими нагріву ящиків, наповнених малотеплопроводным карбюрезатором; забезпечується можливість повної механізації і автоматизації процесу зазнає суттєвого спрощення наступна термічна обробка виробів оскільки можна робити загартування безпосередньо з цементационной печі. Найбільш якісний цементованный шар виходить під час використання в ролі карбюризатора природного газу, який перебуває майже зовсім з метану і пропано-бутановых сумішей, підданих спеціальної обробці, а також рідких углеродов. Основний реакцією, які забезпечують коксування при газової цементації є дисоціація окису вуглецю і метану. Процес ведуть при 910−930 З, 6−12 годин (товщина шару 1−1.7 мм). У серійне виробництво газову цементацию зазвичай проводять у шахтних муфельних печах серії Ц. Шахтні печі серії Ц мають робочу температуру 950 З, одноразову завантаження 185−1100 кг, діаметр робочого простору 300−600 мм висоту 600−1200мм. Вироби в піч завантажують на спеціальних підвісках і пристосуваннях, які вміщують у реторті. Необхідна для газової цементації атмосфера створюється під час подачі до камери печі рідин, багатих вуглецем. Углеводородные сполуки за високої температури розкладаються із заснуванням активного вуглецю і водню. На підприємствах, із серійним масштабом виробництва також застосовують полярні універсальні печі з герметизированной форкамерой і закалочным баком. У таких печах виключається контакт нагрітих деталей з повітрям, запобігається освіту дефектів лежить на поверхні виробів, знижують міцність. У крупносерийном та масовому виробництві газову цементацию проводять у безмуфельных печах безперервного дії. У цих установках весь цикл химико-термической обробки (цементація, гарт і неприйнятно низький відпустку) механізована і автоматизовано; продуктивність установок сягає 500−600 кг/ч і більше. У печах безперервного дії і камерних печах для цементації застосовують эндотермическую атмосферу, у якому додають природного газу (92−95% эндогаза і 3−5% газу). Ендотермічна атмосфера виходить частковим спалюванням газу чи іншого вуглеводнів у спеціальній эндотермическом генераторі при 1000−1200 З у присутності каталізатора. При невеличкому змісті в эндотермической атмосфері СН4 (до 5,0%) не бере участь у процесі насичення вуглецем, а збільшує вміст у атмосфері ЗІ. У умовах лежить на поверхні стали мало виділяється сажа і зберігається однозначна залежність між вуглецевим потенціалом і змістом Н2О і СО2 у атмосфері. Для скорочення тривалості процесу у промисловості широко використовують газову цементацию, коли він вуглецевий потенціал эндотермической атмосфери на початку підтримують високим, які забезпечують одержання поверхневою зоні стали 1,2−1,3% З, та був його вуглецевий потенціал знижують до 0,8%. У печах безперервного дії передбачені дві зони за довжиною печі. У першу зону, приблизно відповідну 2/3 довжини печі, подають газ, який складається з суміші природного і эндотермического газів. По-друге зону подають лише эндотермический газ, що у рівновазі із заданою концентрацією вуглецю лежить на поверхні, зазвичай 0,8% З. під час використання цього цементації слід пам’ятати, що зниження вмісту вуглецю в шарі від 1,2−1,3% до 0,8% відбувається з допомогою вуглецю, розчиненої в аустените. Що стосується легованої стали зниження аустените концентрації вуглецю і легуючих елементів приводить до зменшення закаливаемости і прокаливаемости цементованного шару і врешті-решт погіршення механічних властивостей оброблюваного вироби. У процесі газової цементації в сталь може дифундувати що у атмосфері кисень. Це спричиняє окислювання поверхневого шару стали, товаришів із більшим хімічним засобом до кисню проти залізом. Окислювання легуючих елементів («внутрішнє окислювання») знижує стійкість аустеніту, і за наступної загартуванню в цементованном шарі трооститная сітка і окисли, що знижує його твердість і межа витривалості стали. Добавки і цементуючою атмосфері (наприкінці процесу) аміаку зменшує шкідливий вплив внутрішнього окислення. Швидкість газової цементації за нормальної температури 930−950 З становить 0,12−0,15 мм/ч при товщині шару до 1,5−1,7 мм.
Розробка технології виготовлення детали.
У мартенівських печах виробляють рідкий метал з разливой в зливку. Злиток піддають попередньої термічній обробці, що складається з високого відпустки. Минає зниження внутрішнього напруги, зниження твердості для обдирки зливка. Дялее виробляємо прокатку і штампування зливка методом гарячої деформації за нормальної температури від 1760 до750 із наступним охолодженням. Після цього треба термічна обробка заготівлі - нормалізація за нормальної температури 880 із наступним охолодженням надворі. При нормалізації відбувається перекристалізація стали, устраняющая грубозернисту структуру. Далі йде очищення від окалини. Потім проводимо правку деталм, після чого слід механічна обробка заготівлі, у час якої виготовляють демаль і далі піддають її цементації. Процес ведуть при 910−930 З 6−12 годин. Остаточні властивості цементованных виробів досягаються внаслідок термічної обробки, виконуваної після цементації. У разі проводиться високий відпустку за нормальної температури 620 із метою запобігання освіти залишкового аустеніту при наступної загартуванню. Гарт проводиться за нормальної температури 820 З. це забезпечує здрібнення збіжжя і повну загартування цементованного шару і часткову перекристаллизацию і здрібнення зерна серцевини. Заключним етапом термічної обробки цементованных виробів переважають у всіх випадках є низький відпустку при 160−180 З перевівши мартенсит гарту в поверхневому шарі в відпущений мартенсит, що знижує напруги. Твердість поверхневого шару після термічної обробки HRC 58−62, а серцевини HRC 30−42. Контроль якості термічної обробки складається з: макроаналізу, який застосовують виявлення неметалічних включень і микроанализа, який дозволяє визначити структуру стали, глибину й твердість цементованного шару. У процесі термічної обробки можливі повідця і коробление деталі. Для перевірки повідці і коробления осьові деталі встановлюють в пристосування між центрвами і з допомогою індикатора визначають биття. Найчастіше контроль якості після термічної обробки виробляють вимірюванням твердості на твердомерах. Контроль якості термічної обробки деталі, виявлення внутрішніх та зовнішніх дефектів металі здійснюється з допомогою магнітного, рентгенівського, люменисцентного, ультразвукового та інших фізичних неразрушающих методів контролю. Після контролю за якістю термічної обробки проводять остаточну механічну обробку, що полягає у проведенні шлифования. Після цього отримують готову деталь. Після термічної обробки структура поверхневого шару даного розподільного валу — відпущений мартенсит + карбиды (можливо збереження залишкового аустеніту, але щодо його розкладання після цементації застосовують високий відпустку за нормальної температури 620 З). Серцевина деталі складається з феррита і мартенситу. Ця термічна обробка забезпечує високу твердість цементованного шару, міцність і достатню в’язкість сердцевины.
Можливі причини шлюбу термічної обработки.
До основним дефектів, які можуть виникнути при термічній обробці сталей ставляться тріщини в виробі, внутрішні чи зовнішні, деформації і коробление.
Тріщини. При загартуванню тріщини творяться у тому випадку, коли внутрішні розтягують напруги першого роду перевищують опір стали відриву. Тріщини утворюються за нормальної температури нижче точки Мм, частіше після охолодження. Прихильність до освіті тріщин зростає збільшенням в стали змісту вуглецю, підвищенням температури гарту й збільшенням швидкості охолодження в температурному інтервалі мартенситного перетворення. Інший причиною освіти тріщин є у излделии концентраторів напруг (різку зміну перерізу вироби чи місцеві вирізки, поглиблення, виступи). Тріщини — невиправний дефект. Щоб запобігти етапі їх утворення рекомендується при конструюванні виробів уникати різких виступів, загострених куточків, різких переходів від товстих перетинів до тонким тощо. проводити загартування з максимально низьких температур;осуществлять повільне охолодження в мартенситном інтервалі температур шляхом гарту у двох середовищах, ступінчасті гарту чи застосувати изотермическую загартування; відпустку виконувати немедолнно після закалки.
Деформації і коробления. Деформація, тобто. зміна ж розмірів та форми виробів відбувається за термічної обрабоке внаслідок термічних і структурних напруг під дією неоднорідних об'ємний змін, викликаних нерівномірним охолодженням і фазовыми перетвореннями. Несимметричную деформацію издеилй на практиці часто називають короблением. Воно частіше спостерігається при нерівномірному і надмірно високому нагріванні під загартування, неправильному становищі деталі після занурення у закалочную середовище, й високу швидкість охолодження в мартенситном інтервалі температур. Усунення цих причин значно зменшує коробление. Розміри виробів після гарту навіть за відсутності коробления не совподают з вихідними значеннями. Викликувану цим деформацію можна зменшити добором відповідного складу сталі та умов термічної обробки (зокрема, застосуванням степенчатой і изотермической закалки) Виды шлюбу при цементації та засоби її устранения.
Существуют різні види шлюбу: 1. надмірно велика глибина цементованного шару. Спричинено це: завищене час витримки при цементації, застосування активного карбюризатора, висока температура цементації, нерівномірна температура в печи. при завищеною глибині цементації шлюб неустраним. 2. Занижена глибина цементованного шару. Причини: недостатнє час витримки при цементації, застосування недостатньо активного карбюризатора, занижена температура цементації, нерівномірна температура в печі, недостатня подача газу чи гасу у разі газової цементації. 3. Підвищена концентрація вуглецю в цементованном шарі. Причини: застосування активного карбюризатора і завищене час витримки при цементації. Заходи попередження: дотримання технологічного процесу. 4. Понижени концентрація вуглецю в цементованном шарі. Причины: применение недостатньо активного карбюризатора. 5. Нерівномірна глибина цементованного шару. Причини: зажиренная і брудна поверхню вироби, неправильна упаковка цементационных ящиків, відкладення сажі при газової цементації. 6. Відшаровування загартованого цементованного шару. Причина: різкий перехід від цементованного шару до серцевині, наявність цементитной сітки. 7. Крихкість (выкрашивание поверхового цементованного шару). Спричинено це шлюбу: застосування активного карбюризатора, завищене час витримки. 8. Склоподібні напливи лежить на поверхні виробів. Причини: наявність кварцевого піску в карбюризаторе. Заходи попередження цього шлюбу: недопущення влучення кварцевого піску в карбюризатор.
7. Заходи з техніці безпеки при термічної обработке.
7,1 Вимоги, які пред’являються будівлям і помещениям Здания, у яких містяться термічні цеху, відділення, дільниці мають розташовуватися стосовно найближчим жилим і суспільною будівлям з подветренной боку стосовно які панують у літній час вітрам. Термічні цехи і інші підрозділи термічного виробництва, як правило, повинні розташовуватися в одноповерхових, окремо що стоять будинках. Допускається у виняткових випадках розміщувати термічні підрозділу верхньому поверсі багатоповерхових будинків. Стіни приміщень термічних цехів мали бути зацікавленими вирізняються вогнетривкої фарбою. Підлогу термічних цехів мали бути зацікавленими огнестойкими, рівними, нескользкими і легко очищаемыми від забруднень, при застосуванні у виробництві хімічно активних речовин поли мали бути зацікавленими виготовлені з матеріалу, стійкого проти хімічного воздействия.
7,2 Умови безпечного труда Рабочее виробництво печей для газової цементації має бути герметичним воизбежание вибуху газоподібні карбюризаторы повинні подавалься в піч при температурі печі не нижче 800 З. печі мали бути зацікавленими обладнані спеціальним пристроєм це про людське відведених газів та його дожигания. При поверхневою загартуванню виробів із застосуванням газопламенного нагріву мають дотримуватися діючі «Правила техніки безпеки і виробничої санітарії під час виробництва ацетилени, кисню і газопламенной обробці металів». Робітники місця повинні прагнути бути обладнані місцевої механічної витяжкою. Витяжні труби слід забезпечити максимальний паркан що виділяються шкідливих газів від місць етапі їх утворення. Робоча місце має бути організовано таким чином, щоб робочі в усі час займали становище обличчям по вхідному отвору витяжних пристроїв. Приміщення, у якому виробляється полум’яна поверхнева гарт виробів мусить бути обладнана общеоюменной вентиляцією. Очищення виробів після обробки повинна перевірятися в гидропескоструйных камерах, соціальній та дробеструйных, дробеметных установках і установках для очищення металевим піском. Використання пескоструйных апаратів з застосуванням сухий пескоочистки деталей запрещается.
7,3 Оборудование Оборудование термічних цехів повинно міститися відповідно до загальним напрямом основного вантажопотоку. Відстань між обладнанням і стінами цеху має не меншим як один метр. Устаткування, під час роботи якого виникає шум, перевищує санітарні норми, має шумоизолироваться чи встановлюватися в ізольованих приміщеннях. Виробничі процесся, що супроводжуються забрудненням повітря робочої зони шкідливими виділеннями різних парів, газів і пилу, якщо вони розташовані поза потоку, мали бути зацікавленими відділені з інших учасників термічної обробки, а обладнання має бути снабжено місцевими отсосами чи іншими устройствами.
Заключение
.
У цьому курсової роботі був розібрано процес виготовлення розподільного валу. Запропоновано схема маршрутної технології виробництва деталі, розроблено режими термічної обробки, щоб забезпечити необхідний рівень механічних властивостей металу. Діяльність обгрунтоване застосування стали 20Х виготовлення розподільного валу і запропоновані її замінники. Також запропонована термограма технологічного процесу деталі, розглянуті можливі причини шлюбу термічної обробки, вказані заходи щодо техніці безпеки при термообработке.
Список використовуваної литературы.
1. Лахтин Ю. М., Леонтьєва В.П. Матеріалознавство. Підручник для вузів — М. 2. Марочник сталей і сплавів. / В. Г. Сорокін, А. В. Волосникова,.
С.А.Вяткин та інших. / під ред. В. Г. Сорокіна. — М.: Машинобудування, 1989.
— 640с. 3. В.М. Зуєв. Термічна обробка металів: Підручник для середовищ. ПТУ.,.
1986. — 288с. 4. Деталі машин / Ю. Н. Березовський, Д.В. Чернілевський, М. С. Петров.
/ під ред. Н.А. Бородіна. — М.: Машинобудування, 1933. — 384с. 5. Фиргер І.В. Термічна обробка сплавів; Довідник. — М.
Машинобудування, 1982. — 304с., ип (серія довідників для рабочих).