Установка гідроочистки дизельного палива
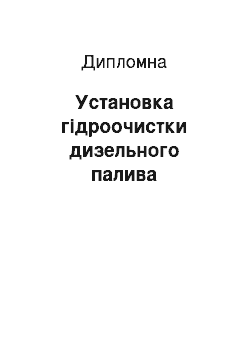
Разом з цільовим дизельним паливом утворюється до 1−2 мас.% низькооктанового бензину, що використовується як добавка до сировини каталітичного риформінга, до 1,5−3 мас.% сірководню (сировина для виробництва сірки і сірчаної кислоти) і невелика кількість (0,5−1,0 мас.%) вуглеводневих газів. Склад вуглеводневих газів звичайно буває наступним (у мас.%): Метан — 50; Етан — 30; пропан — 12; ізобутан… Читати ще >
Установка гідроочистки дизельного палива (реферат, курсова, диплом, контрольна)
Реферат
Пояснювальна записка до дипломного проекту: с. 96, рис. 10, табл. 19, літературних джерел 18, креслень 5 .
Об'єкт дослідження — установка гідроочистки дизельного палива.
Мета роботи — проект блоку гідроочистки дизельного палива установки Л-24−7 з розробкою заходів по підвищенню якості гідрогенізату, спеціальна частина — розрахунок основного обладнання.
В дипломному проекті наведено аналітичний огляд процесів гідроочистки дизельного палива, розглянуто фізико — хімічні основи процесу, представлена характеристика сировини, каталізатора, готової продукції. Вибрана та описана технологічна схема, приведений матеріальний баланс процесу, виконані технологічні розрахунки реакторного блоку.
У розділі «Автоматичні системи керування технологічним процесом» розроблена функціональна схема автоматичного контролю та регулювання блоку гідроочистки.
У розділі «Охорона праці» розробленні необхідні заходи по техніці безпеки, промислової санітарії та протипожежної безпеки.
У розділі «Економіка та організація підприємства» приведено розрахунок собівартості однієї тони гідроочищеного дизельного палива
Гідроочистка, дизельне паливо, реактор, каталізатор, водневмістний газ, сірководень.
Зміст
Вступ
1. Аналітичний огляд методів виробництва процесу гідроочистки
1.1 Процеси гідроочистки дизельного палива
1.2 Каталізатори гідроочистки
2. Фізико-хімічні основи процесу гідроочистки
2.1 Основні параметри процесу гідро очистки
2.1.1 Температура процесу гідро очистки
2.1.2 Тиск процесу гідро очистки
2.1.3 Об'ємна швидкість подачі сировини
2.1.4 Співвідношення водень/сировина
2.2 Опис хімічних реакцій
2.2.1 Гідрогеноліз сполук сірки
2.2.2 Гідрогеноліз сполук азоту
2.2.3 Гідрогеноліз сполук кисню
2.2.4 Гідрування ароматичних та поліароматичних вуглеводнів
2.2.5 Гідрогенізація олефінів
2.2.6 Гідрокрекінг
2.2.7 Конденсація ароматичних вуглеводнів
3. Характеристика сировини, реагентів, готової продукції
4. Вибір, обґрунтування та опис технологічної схеми
5. Технологічні розрахунки
5.1 Матеріальний баланс установки
5.1.1 Вихід гідроочищенного дизельного палива
5.1.2 Витрати водню на гідроочистку
5.1.3 Втрати водню з віддухом
5.1.4 Матеріальний баланс установки
5.1.5 Матеріальний баланс реактору
5.1.6 Тепловий баланс реактору
5.1.7 Механічний розрахунок реактора
6. Автоматичний контроль та керування технологічним процесом
6.1 Аналіз об'єкту керування
6.1.1 Короткий опис об'єкту керування
6.1.2 Задачі контролю та керування технологічним процесом
6.2 Розробка системи керування технологічним процесом
6.2.1 Призначення, цілі та функції системи керування
6.2.2 Вибір комплексу технічних засобів
6.2.3 Опис функціональної схеми системи керування
7. Охорона праці
7.1 Характеристика проектуємого об'єкту та місця його розташування
7.2 Характеристика небезпечних та шкідливих виробничих факторів на проектуємій установці
7.3 Заходи по створенню безпечних і здорових умов праці, передбачених проектом
8. Організаційно-економічна частина
8.1 Розрахунок виробничої програми
8.2 Розрахунок показників роботи обладнання
8.3 Розрахунок капітальних вкладень
8.4 Розрахунок чисельності та оплати праці персоналу для капітального будівництва
8.5 Розрахунок собівартості виробництва
8.6 Розрахунок економічної ефективності проектного рішення Висновки Література Додаток
Вступ
Згідно відомо, що один з найпоширеніших процесів нафтопереробки — гідроочистка моторних палив, тому що з її допомогою досягається поліпшення якості бензинів, керосинів, дизельних палив і з’являється можливість регулювання на заводах співвідношення вироблених кількостей різних моторних палив.
Розвиток важкої промисловості, транспорту, сільського господарства та інших галузей викликав потребу в збільшенні виробництва палив і змащувальних мастил, а отже і збільшення ресурсів вуглеводневої сировини — газоподібних і рідких нафтопродуктів.
В результаті гідрогенізаційного облагороджування (гідроочистки) знижується вміст сірчистих сполук в бензинових, гасових і дизельних фракціях. Застосування гідроочистки для підготовки сировини каталітичного крекінгу і гідроізомерізації для облагороджування бензинових, дизельних і реактивних дистилятів дозволяє одержувати палива із значно кращими характеристиками.
Гідроочистка дизельного палива займає важливе місце у виробництві малосірчистого дизельного палива, що виробляється з сірчистих гасогазойлевих дистилятів. Для облагороджування дизельних палив використовують більше 30% світової потужності установок гідроочистки.
Процес здійснюється на стаціонарному каталізаторі. Найбільш широко застосовують алюмокобальтмолібденовий каталізатор; в його присутності був детально вивчений вплив основних параметрів процесу на видалення сірчистих сполук з дизельного палива, в середовищі воденьвмісного газу в умовах, при яких 97−99%(мас.) вихідної сировини перетворюється в очищений продукт. Одночасно утворюється незначна кількість бензину. Каталізатор періодично регенерують.
1. Аналітичний огляд методів виробництва процесу гідроочистки
Гідроочистку прямогінних фракцій проводять лише для видалення сірчистих сполучень; це можна здійснювати при відносно невисокому парціальному тиску водню в процесі.
Для досягнення глибини гідроочистки 80−90% достатньо підтримувати парціальний тиск водню до 30 МПа. Решта умов процесу — температура 350−400 °С, питома об'ємна швидкість подачі сировини 2−5,0г-1, питома циркуляція газу 300−600 мі/мі сировини — встановлюють залежно від характеристики початкової сировини і необхідної глибини знесірчування. Вуглеводневий склад палива змінюється при гідроочистки трохи, і цетанове число продукту зростає на 1−2. Для отримання дизельного палива з цетановим числом не менше 45 потрібна зміна умов гідроочистки і в першу чергу величини парціального тиску водню, тобто необхідний процес гідрування.
Був детально вивчений вплив основних параметрів процесу на гідроочистку суміші в співвідношенні 1:1 фракцій 200−350 °С прямогінної і дистиляту каталітичного крекінгу. Початкова сировина містила 1,3 мас.% сірі, 33 об.% вуглеводнів, що сульфують, мале йодне число 12 і цетанове число 45. Процес проводили на алюмокобальтмолібденовому каталізаторі. У міру збільшення температури процесу гідроочистки при загальному тиску 40 МПа і подачі воденьвмісного газу (із змістом водню 65 об.%) 500 мі/мі ступінь гідрування сірчистих сполук і неграничних вуглеводнів зростає, досягаючи максимальної величини при температурі близько 420 °C. При подальшому підвищенні температури глибина гідрування сірчистих сполук знижується трохи, а ненасичені вуглеводнів — досить різко.
У міру збільшення температури з 300 до 380−420 °С вміст вуглеводнів, що сульфують, в гідрогенізаті зменшується з 33 до 30−31 об.%, а при подальшому підвищенні температури до 460 °C дещо збільшується внаслідок часткової дегідрогенізації нафтенових вуглеводнів. Відповідно до цього при підвищенні температури з 300 до 380 °C цетанове число палива зростає на 1−2, а при подальшому зростанні температури починає дещо зменшуватися.
Підвищення парціального тиску водню, так само як і зниження питомої об'ємної швидкості подачі сировини, сприяє збільшенню глибини гідрування сірчистих сполук і ненасичених вуглеводнів. Процес проводили при 380 °C, питомий об'ємній швидкості подачі сировини 1,0 г-1 і подачі газу (що містив 65 об.% водню) 500 мі/мі сировини. Підвищення парціального тиску водню до визначеного викликає різке збільшення глибини гідрування сіркоорганічних сполук; подальше ж збільшення тиску практично не відображається на ступені очищення.
Парціальний тиск водню і умовний час контакту сировини з каталізатором визначаються кількістю що подається в реакційну зону воденьвмісного газу.
В цих умовах глибина гідроочистки невисока, і кількість водню, що подається, дозволяє достатньо чітко прослідити її зміну. В таких умовах максимальна глибина гідроочистки прямогінного дизельного палива досягається при питомій подачі водню 500 мі/мі сировини. При зменшенні питомої подачі водню парціальний тиск водню знижується, внаслідок чого, не дивлячись на збільшення умовного часу контакту сировини з каталізатором, глибина гідроочистки зменшується.
При здійсненні процесу гідроочистки дизельного палива під тиском 40−50 ат найближча оптимальна питома подача воденьвмісного газу — 250−600 мі/мі сировини.
Разом з цільовим дизельним паливом утворюється до 1−2 мас.% низькооктанового бензину, що використовується як добавка до сировини каталітичного риформінга, до 1,5−3 мас.% сірководню (сировина для виробництва сірки і сірчаної кислоти) і невелика кількість (0,5−1,0 мас.%) вуглеводневих газів. Склад вуглеводневих газів звичайно буває наступним (у мас.%): Метан — 50; Етан — 30; пропан — 12; ізобутан — 3 і н_ бутан — 5. Витрата водню в процесі гідроочистки залежить від якості початкової сировини і глибини його знесірчування і звичайно знаходиться в межах 0,5−1 мас.% на сировину. Як воденьвмісний газ застосовують головним чином газ каталітичного риформінга.
1.1 Процеси гідроочистки дизельного палива
У даному підрозділі розглянуто де які принципові схеми установок [ 5 ]
Установка Л-24−7
Призначення. Знесірчування прямогонних дизельних фракцій з нафт типу арланскої із вмістом сірки 2,4% (мас). Можливо застосування як сировина суміші прямогінних і вторинних дизельних фракцій в співвідношенні 1:1 із вмістом сірки 1,3% (мас).
Опис установки (рисунок 1.1). Установка складається з двох самостійних блоків, що дозволяють одночасно переробляти два види сировини.
Сировина насосом подається на вузол змішення з циркуляційним воденьвмісним газом. Газосировинна суміш нагрівається в теплообмінниках і в печі і поступає в два послідовно працюючих реактора. Газопродуктова суміш, пройшовши теплообмінники і холодильники, прямує в сепаратора високого тиску, де циркуляційний газ відділяється від гідрогенізату; після очищення від сірководню 15% розчином МЕА подається на компресор. Кожний блок має самостійну систему циркуляції газу. Вузол регенерації розчину МЕА загальний для двох блоків.
Гідрогенізат і розчинені гази з сепаратора високого тиску дроселюють до 0,6 МПа в сепаратора низького тиску. Гідрогенізат, заздалегідь нагрітий в теплообмінниках, поступає на стабілізацію.
Технологічна схема установки Л24_7
Вуглеводневий газ, обчищений розчином МЕА від сірководня, дроселює до 0,14 МПа і об'єднується з обчищеним вуглеводневим газом стабілізації, дожимається компресором до 1,0 МПа і видається з установки.
П — трубчаста піч; Р — реактори; Т — теплообмінники; К — колони; Г — газосепаратори; Н — насоси; Сскрубер; ВКвідгінна колона 1 — початкова сировина; 2 — воденьвмісний газ; 3 -воденьвмісний газ що віддувається; 4 — бензин; 5 — дизельне паливо; 6 — сірководень; 7 — газ стабілізації.
Рисунок 1.1-Технологічна схема установки Л24_7
Частина дизельного палива (рециркулят) відцентровим насосом подається через трубчасту піч назад в стабілізаційну колону, а решта кількості прокачується через теплообмінники, холодильник і поступає на «защелачивание» і водну промивку, а потім в товарний парк. Якщо режим колони забезпечує повне видалення сірководню з дизельного палива, то можна працювати без «защелачивания» і водної промивки стабільного палива.
МЕА, насичений сірководнем, збирається від абсорберів в загальний потік, нагрівається в теплообмінниках і поступає в відгінну колону. Сірководень разом з парами води, що виділився, охолоджується в конденсаторі-холодильнику і поступає в сепаратора, де від нього відділяється вода, яка повертається в колону на зрошування. Сірководень, що утворюється, виводиться з установки для отримання сірчаної кислоти або елементарної сірки. Регенерований розчин МЕА після охолоджування в теплообміннику і холодильнику повертається в цикл. Температуру в нижній частині відгінної колони підтримують подачею пари в рибойлер.
Для відновлення активності каталізатора його піддають періодичній газоповітряній регенерації роздільно для кожного блоку.
Основне устаткування. Реактор з аксіальним введенням сировини зверху вниз. Корпус реактора футеровано зсередини; реактор не має захисного стакана. Діаметр реактора 2600 мм Продуктово-сировинні теплообмінники кожухотрубчасті Діаметр корпусу 1200 мм.
Продуктовий холодильник високого тиску кожухотрубчастий.
Трубчасті печі шатрового типу із зварним змійовиком в зоні вогняного нагріву.
Компресори циркуляційного газу поршневого типу.
Колонні апарати різного діаметра з S-образними тарілками або насадкою з кілець Рашига.
Установка Л-24−2000
Призначення. Гідроочистка прямогонних дизельних фракцій з нафт типу ромашкинской.
Опис установки (рисунок 1.2). Сировина змішується з циркуляційним водневмісним газом, що нагнітається відцентровим компресором
Технологічна схема установки ЛЧ24_2000.
Газосировинна суміш нагрівається спочатку в теплообмінниках потоком стабільного палива, що поступає з нижньої частини стабілізаційної колони, потім в теплообміннику потоком газопродуктової суміші, в печі і прямує в реактор. Після реактора газопродуктова суміш віддає своє тепло газосировинної суміші і подається в гарячого сепаратора. Парогазова суміш з гарячого сепаратора використовується для нагріву гідрогенізату з холодного сепаратора і отримання водяної пари в рибойлорі.
П — трубчаста піч; Р — реактор; Т — теплообмінники; Х — повітряний холодильник; КС — стабілізаційна колона; С — сепаратори; Н — насос; 10 — колона для віддува сірководню з бензину; А — абсорбери; ВК — відгінна колона; 1 — сировина; 2 — воденьвмісний газ; 3 — УВ газ; 4 — бензин; 5 — дизельне паливо; 6- сірководень; 7 — газ стабілізації; 8 — УВ газ до печей.
Рисунок 1.2- Технологічна схема установки Л24_2000
Потім суміш газу і нафтопродукту охолоджується послідовно в повітряному і водяному холодильниках і поступає в холодного сепаратора, де виділяється циркуляційний воденьвмісний газ. Гідрогенізат з холодного сепаратора, заздалегідь нагрітий в теплообміннику парогазовою сумішшю з гарячого сепаратора, змішується з гідрогенізатом з гарячого сепаратора і прямує в колону стабілізації.
Циркуляційний газ піддається очищенню від сірководню і повертається в цикл. Для підтримки потрібної концентрації водню в циркуляційному газі перед сепаратором на компресор постійно подасться свіжий воденьвмісний газ, а частина циркуляційного газу відбуває. Воденьвмісний газ, що віддуваєтся, заздалегідь нагрітий в підігрівачі печі, прямує в стабілізаційну колону з метою зниження парціального тиску пари нафтопродукту. В колоні з дизельного палива виділяються вуглеводневі гази і бензин для отримання дизельного палива з необхідною температурою спалаху. Тепловий режим колони забезпечується теплотою сировини, що подається в стабілізаційну колону.
Стабільне дизельне паливо, що виходить з нижньої частини колони охолоджується в теплообмінниках і повітряному холодильнику, після чого виводиться з установки. З верху колони відбирається бензин і вуглеводневий газ; після охолоджування вони поступають до сепаратора, в якому бензин відстоюється від водного конденсату. Очищення бензину від сірководню здійснюється шляхом його продування в колоні очищеним вуглеводневим газом. Водяний конденсат прямує в деаератор для віддува сірководню водяною парою. Конденсат, звільнений від сірководню, після охолоджування скидається у виробничу каналізацію, а сірководень — у факельну лінію.
Вуглеводневий газ очищається від сірководню розчином МЕА і використовується як паливо для печі. Насичений кислими газами розчин МЕА дегазується при зниженому тиску і прямує на десорбцію в відгінну колону. Температурний режим в колоні підтримується циркулюючим через термосифонний паровий рибойлер розчином МЕА. Сірководень, що утворюється, виводиться з установки для отримання сірчаної кислоти або елементарної сірки. Механічні домішки віддаляються з частини регенерованого розчину МЕА фільтруванням через фільтр з намивним шаром. Для запобігання вспінювання розчину МЕА на тарілках абсорберів в систему подається антивспінювач.
При падінні активності каталізатора проводиться його газоповітряна регенерація по замкнутому циклу із застосуванням содового розчину.
Основне устаткування. Реактор з аксіальним введенням сировини зверху вниз. Корпус виконаний з двошарового металу; передбачена зовнішня ізоляція. Діаметр реактора 3600 мм Трубчаста піч вертикально-секційного типу, що складається з двох секцій, кожна з яких має радіантну і конвекційну камери. В конвекційній частині розташований змійовик нагріву газу для віддува в стабілізаційну колону. Для опалювання печей використовується вуглеводневий газ, одержуваний в процесі.
Сировинний теплообмінник кожухотрубчастий з плаваючою головкою, одноходовою; ущільнення — сильфонний компенсатор. Діаметр корпусу 1300 мм.
Повітряні холодильники типу АВГ з коефіцієнтом оребрення 22.
Стабілізаційна колона з клапанними тарілками. Число тарілок _25.
Колони очищення циркуляційного і вуглеводневого газу стабілізації, а також відгінна колона з S-образними тарілками.
Секція 300−1 установки ЛК-6У
Призначення. Гідроочистка прямогінних дизельних фракцій і нафт типу ромашкінскої.
Опис секції гідроочистки (рисунок. 1.3). Сировина подається на змішення циркуляційним газом і воденьвмісним газом, що поступає з секції 300−2 (гідроочистка гасу).
Технологічна схема Секції 3001 установки ЛК_6У
Газосировинна суміш нагрівається в теплообмінниках, потім в трубчастій печі до температури реакції і поступає в реактор. Газопродуктова суміш з реактора подається па нагрів газосировинної суміші, потім частина потоку — 70% (мас.) — прямує в теплообмінник блоку стабілізації, де нагрівається сировина для стабілізаційної колони. Подальше охолоджування газопродуктової суміші здійснюється в повітряному холодильнику, а охолоджування до 38 °C — у водяному холодильнику. Розділення нестабільного гідрогенізату і циркуляційного газу відбувається в сепараторі високого тиску, звідки нестабільний гидрогенизат, заздалегідь нагрітий за рахунок теплообміну з газопродуктовою сумішшю, дроселює в стабілізаційну колону.
П — трубчаста піч; Р — реактор; Т — теплообмінники; Х — холодильник; С — сепаратори; К — стабілізаційна колона; Н — насоси; А — абсорбери; ВК — відцентровий компресор; 1 — сировина; 2 — воденьвмісний газ; 3 — газ що віддувається з секції 300−2; 4 — воденьвмісний газ з секції 300−2; 5 — газ що віддувається; 6 — насичений розчин МЕА з секції 3002; 7 — бензин; 8 — ДП; 9 — вуглеводневий газ; 10- вуглеводневий газ з секції 300−2; 11 — регенерований розчин МЕА; 12 — насичений розчин МЕА.
Рисунок 1.3- Технологічна схема Секції 3001 установки ЛК_6У Стабілізація гідрогенізату здійснюється водяною парою, яка подається в нижню частину колони для зниження парціального тиску пари нафтопродуктів і вуглеводнів. Пари бензину, водяна пара і газ виводяться з колони, охолоджуються і розділяються в сепараторі. Бензин з сепаратора частково повертається і колону на зрошування, а балансова кількість змішується з бензином, що поступає з секції 300_ 2, і прямує на віддув сірководню вуглеводневим газом. Очищений бензин подається або в секцію 200 (риформінг), або в секцію 100 (ЕЛОУ-АТ).
Вуглеводневий газ очищається від сірководню спільно з вуглеводневим газом секції 300−2. Потім газ частково прямує для віддува сірководню з бензину, а решта кількості - в паливну сіть. Вуглеводневий газ після колони віддува сірководню з бензину також очищається від сірководню.
Вода, одержувана в процесі і від конденсації пари, заздалегідь нагріта в теплообміннику, поступає в відпарну колону. Тепловий режим колони підтримують подачею гострої пари. Обчищена охолоджена вода скидається в каналізацію; відпарені гази віддаляються в димар.
Стабільна очищена фракція охолоджується послідовно в теплообміннику, повітряному холодильнику і з температурою 50 °C виводиться з установки.
Гази очищаються 15% розчином МЕА. Регенерацію розчину МЕА в секції не здійснюють.
Основне устаткування. Реактор з аксіальним введенням сировини зверху вниз. Корпус реактора виконаний з двошарової сталі без внутрішньої футеровки. Діаметр реактора 3500 мм Сировинні теплообмінники кожухотрубчасті з лінзовим компенсатором на плаваючій головці, противоточні.
Повітряні холодильники зигзагоподібного типу з коефіцієнтом оребрення 22.
Трубчасті печі вертикально-секційного типу з тепловим навантаженням 43,7 МВт.
Турбокомпресор циркуляційного газу з електроприводом (без резерву).
Колонні апарати різного діаметра з клапанними тарілками або насадкою з кілець Рашига.
Насосне устаткування, в конструкції якого передбачена можливість повної автоматизації. Насоси встановлені на відкритому майданчику.
1.2 Каталізатори гідроочистки
гідроочистка дизельний паливо гідрогенізат В процесі гідроочистки дизельного палива можуть бути використані будь-які сіркостійкі гідруючі каталізатори, але кращі результати дають метали, оксиди і сульфіди елементів VI або VIII груп періодичної системи елементів (нікель, кобальт, залізо, молібден, вольфрам, хром) і різні їх поєднання один з одним.
Згідно з [3 ] відомо, що промисловості широко поширені каталізатори: поєднання оксидів і сульфідів кобальту з оксидами і сульфідами молібдену або вольфраму, а саме молібдатів кобальту, сульфовольфроматів нікелю і т.д. Як носій, найбільш вживається активний окисел алюмінію в чистому вигляді.
Склад каталізаторів гідроочистки, зокрема алюмокобальтмолібденових, робить істотний вплив на їх активність і селективність. При цьому важливий не тільки загальний вміст оксидів кобальту і молібдену в каталізаторі, але і співвідношення між ними. Мольне відношення оксидів кобальту і молібдену може мінятися від 0,2:1 до 5:1. Найбільш часто це відношення рівно 1:1.
В алюмокобальтмолібденових каталізаторах мольні відносини оксидів нікелю і молібдену складають 0,5ч1,15:1. В нікельвольфрамових каталізаторах мольне співвідношення компонентів рівно 0,5ч2:1.
Оптимальний вміст активних гідруючих компонентів в кобальтмолібденових і нікельмолібденових каталізаторах складає 820 мас.%. Подальше збільшення цих компонентів приводить лише до незначного підвищення активності каталізатора. Результати досліджень показали, що зразки каталізаторів, що містять 3,2−8,9. мас. % СоО і 17,210, 7 мас. % МоО2, по здатності, що знесірчує, близькі між собою.
Істотний вплив на механічні властивості, активність, селективність і стабільність каталізаторів гідроочистки надають способи їх приготування.
Активні системи — молібдати кобальту (нікелю) готують з розчинів солей, що містять еквімолекулярні кількості оксидів молібдену і кобальту, з подальшими операціями відділення, промивки і висушування осаду. Отриманий молибдат кобальту (нікелю) змішують з окислом алюмінію і піддають термічній обробці. Каталізаторну масу фільтрують, формують і піддають термічній обробці. У такий спосіб проводять вітчизняні промислові алюмомолібденовий і алюмокобальтмолибденовый каталізатори.
Вводити активні компоненти до складу каталізатора можна шляхом просочення готового сформованного носія (наприклад, окисли алюмінію)
розчинами, що містять активні компоненти. Просочення можна проводити послідовно, кожним з розчинів солей або розчином, що містить сполучення двох активних компонентів (оксиди молібдену і кобальту). Для цього використовують стабільні розчини комплексних аміачних сполучень молібдену і кобальту, нікелю і вольфраму або нікелю і молібдену при великих надлишках аміаку. Інколи замість розчинів аміаку можна використовувати розчини моноетаноламіну. Після просочення каталізатор висушують і піддають термічній обробці.
Недолік вказаного способу — неоднорідність розподілу гідруючого компоненту від периферії до центру зерна каталізатора внаслідок виборчої адсорбції активного компоненту з розчину на зовнішній поверхні носія і повільній дифузії всередину зерна. Для отримання більш однорідного каталізатора просочений носій подрібнюють, а потім повторно піддають термічній обробці. Такий прийом використаний у виробництві никельвольфрамового сульфідного каталізатора на активному окислі алюмінію.
Встановлено [ 8 ], що алюмокобальтмолібденовий каталізатор найбільш активний при просоченні готового носія змішаним розчином активуючих компонентів.
Істотну роль у формуванні активного, стабільного і механічно міцного каталізатора в промисловому його виробництві грають умови термічної обробки — сушки і прожарення. Оптимальні умови прожарення алюмокобальтмолибденового каталізатора наступні: температура 620−650 °С, тривалість 8−10 г.
Загальновідомо, що висока активність сучасних каталізаторів гідроочищення (каталізаторів серії BRIM™ фірми Haldor Topsoe, серії SENTINEL™ фірми Axens, серії STARS™ фірми Albermarle та серії actiCAT фірми CRITERIONTM) забезпечується наявністю на поверхні каталізатора високодисперсних частинок сульфідної Co (Ni)-Mo ~ S фази Типу II .
В Інституті каталізу СО РАН розроблено оригінальний спосіб отримання високодисперсних сульфідних каталізаторів, заснований на однократному промоченні алюмооксидного носія разчином, що містить біметалічні комплекси Co (Ni) і Мо з хелатними лігандами. Наявність такої структури в оксидній формі каталізатора забезпечує передумови для формування високоактивної дисперсної фази при дотриманні режимів термообробки і сульфідування.
У даній роботі представлені результати дослідження активності нових СоМо / А12О3 і NiМо/ А12О3 каталізаторів, отриманих з використанням хелатних лігандів що характеризуються високою дисперсністю активної сульфідної фази, в реакціях гідрознесірчення і гідродеазотування. Оцінка кінетичних параметрів перетворення сірчистих сполук, дозволила провести чисельні розрахунки та підбір оптимальних робочих режимів процесу гідроочищення (температури, тиску, об'ємної швидкості реакції, кратності циркуляції), необхідних для отримання гідрогенізатів із заданим залишковим вмістом сірки.
Порівняння ефективності використання СоМо/ А12О3 і NiMo/ А12О3 каталізаторів у процесі гідроочищення. На рис. 1.4, 1.5 наведено розрахункові залежності залишкового вмісту сірки та азоту від температури на вході в реактор, а на рис. 1.6,1.7 — від тиску водню для СоМо / А12О3 і NiMo/ А12О3 каталізаторів. NiMo/ А12О3 каталізатор має помітну перевагу перед СоМо/ А12О3 каталізатором в гідродеазотувані у всьому діапазоні робочих умов. У той же час у реакції гідрознесірчення NiMo-каталізатор наближається за ефективністю до СоМо-каталізатору тільки на верхньому робочому значенні температури.
Рисунок 1.4- Вплив температури на залишковий вміст сірки при гідро очистці в присутності CoMo та NiMo каталізаторів У реакції гідрознесірчення NiМо/ А12О3 каталізатор сильніше реагує на збільшення тиску водню, проте поступається за сумарною активністю СоМо-каталізатору.
Рисунок 1.5- Вплив температури на залишковий вміст азоту при гідро-очистці в присутності CoMo та NiMo каталізаторів.
У випадках, коли поряд з високим ступенем гідрознесірчення необхідно досягнення також і високої конверсії азотовмісних, може представляти інтерес застосування комбінованого шару з СоМо/ А12О3 і NiMo/ А12О3 каталізаторів. Як вже зазначалося, NiMo/ А12О3 каталізатор проявляє помітно більш високу активність у гідродеазотуванні. Для забезпечення максимальної ефективності роботи реактора з комбінованим шаром NiMo/ А12О3 каталізатор доцільно завантажувати в хвостову частину шару, що забезпечить максимальну активність в реакції гідродеазотування. Це також скоротить відставання NiMo/ А12О3 каталізатора по активності в реакції гідрознесірчення від СоМо/ А12О3 каталізатора внаслідок більш високої температури на виході з реактора
Рисунок 1.6- Вплив тиску на залишковий вміст сірки при гідроочистці в присутності CoMo та NiMo каталізаторів Аналіз даних про активність російських каталізаторів в реакції гідрознесірчення дозволяє зробити висновок про те, що СоМо/ А12О3 каталізатор нового покоління, забезпечує більш глибоку конверсію сірковмісних сполук у порівнянних умовах.
У результаті проведеного порівняльного дослідження активності СоМо/А12О3 і NiMo/А12О3 каталізаторів нового покоління в реакціях гідрознесірчення і гідродеазотування, типового для російських НПЗ, встановлено, що в заданих умовах СоМо/ А12О3 каталізатор характеризується більш високою активністю в реакціях гідрознесірчення, в той час як NiMo/ А12О3 забезпечує більш високу конверсію азотовмісних сполук.
Рисунок 1.6- Вплив тиску на залишковий вміст азоту при гідро очистці в присутності CoMo та NiMo каталізаторів Для оцінки кінетичних параметрів перетворення сірко-та азотовмісних сполук було проведено тестування каталізаторів у пілотному
реакторі проточного типу з варіюванням температури від 360 до 400 С при об'ємній швидкості подачі сировини 1−4 ч-1, відносно водень / сировина 300−600 нмі/мі і тиску 3,5−6,5 МПа. Розроблено модель, що дозволяє провести підбір оптимальних робочих режимів процесу гідроочищення (температури, тиску, об'ємної швидкості, кратності циркуляції), необхідних для отримання гідрогенізатів із заданим залишковим вмістом сірки.
2. Фізико-хімічні основи процесу гідроочистки
Процес гідроочищення характеризується видаленням сірки з вуглеводневої сировини у вигляді сірководню. Сировина контактує з ВВГ у присутності каталізатора при середньому / високому тиску і температурі. Умови реакції такі, що фракція або повністю переходить в пароподібний стан, або залишається частково в рідкому стані («струменевий режим»).
Вихід продукту реакції високий, оскільки видаляється, фактично, тільки сірка. Крім того, утворюється сірководень який легко і селективно видаляється з продуктових потоків (газоподібних і рідких). Сірководень отримують як потік високої концентрації, який можна переробити в елементарну сірку за технологією Клауса, сірчану кислоту та інші продукти.
2.1 Основні параметри процесу гідро очистки
Основними параметрами процесу гідроочистки є:
— температура в реакторі;
— тиск у реакторі;
— об'ємна швидкість подачі сировини;
— відношення водень/сировина.
2.1.1 Температура процесу гідро очистки
Температура впливає на протікання реакцій процесу гідроочистки. Вплив температури проведення процесу гідроочистки неоднаковий для різних типів реакцій.
Робоча температура процесу гідроочищення в залежності від складу сировини втримується в діапазоні від 315 °C до 385 °C. Максимально припустима температура проведення процесу гідроочистки на каталізаторі складає 400 °C.
Реакція видалення сірки починає протікати при температурі 230 °C. Швидкість реакції видалення сірки з підвищенням температури зростає.
Для розкладання кисень і азотовмісних сполук потрібно ще більш висока температура, ніж для насичення олефінів. При збільшенні кількості даних сполук у сировині необхідно підвищувати температуру проведення процесу.
На початку циклу роботи каталізатора необхідно установити мінімальну температуру (не нижче 315°С), що забезпечує необхідну якість сировини. В міру падіння активності каталізатора якість гідрогенізату погіршується. Для підтримки заданої якості гідрогенізату (вміст сірки й азоту) підвищують температуру на вході в реактор Р-1 блоку гідроочистки.
2.1.2 Тиск процесу гідро очистки
Глибина протікання реакцій гідроочистки росте зі збільшенням парціального тиску водню, що залежить від загального тиску в системі, витрати ВВГ, що подається і концентрації водню в ньому. Крім того, при високих тисках каталізатор довше зберігає свою активність.
Зниження витрати ВВГ, концентрації водню, тиску в системі веде до швидкого коксування каталізатора.
2.1.3 Об'ємна швидкість подачі сировини
Об'ємна годинна швидкість подачі сировини визначається відношенням обсягу сировини, що подається до реактору за одну годину, до обсягу
каталізатора, завантаженого в реактор:
Зі збільшенням об'ємної швидкості зменшується час перебування сировини в реакційній зоні (час контакту сировини з каталізатором). При цьому підвищується продуктивність і зменшується глибина очищення сировини. При зниженні об'ємної швидкості збільшується час контакту сировини з каталізатором і зростає глибина очищення сировини. Однак при цьому зменшується продуктивність, зростає коксоутворення, знижується тривалість роботи каталізатора.
2.1.4 Співвідношення водень/сировина
При теоретично розрахованих кількостях водню реакції видалення сірки в процесі гідроочистки можуть протікати майже цілком, але швидкість їхнього протікання дуже мала. Тому процес гідроочистки ведуть при надлишковій кількості водню.
Мінімальне відношення водень/сировина для блоку гідроочистки дорівнює 225 нмі/мі. При збільшенні відношення водень/сировина швидкість реакцій процесу гідроочистки зростає. Збільшення відношення водень/сировина понад 500 нмі/мі уже не впливає на швидкість реакцій гідроочистки. Для видалення азоту, сірки необхідна чистота водню не нижче 70% .
2.2 Опис хімічних реакцій
Крім гідрознесірчення [5], на процес впливають такі реакції: гідрування аренів та олефінів, гідрокрекінг і, в деякій мірі, утворення коксу.
Також враховується гідрогеноліз сполук, що містять азот і кисень, здебільшого істотно підвищує якість продукту, хоча його ефект для виробництва буде, в цілому, мізерний, з урахуванням того, що ці сполуки, в порівнянні з тими, які містять сірку, присутні у відносно невеликих кількостях.
2.2.1 Гідрогеноліз сполук сірки
У процесах гідроочищення, в яких видалення сірки є головним завданням, реакціями, що представляють головний інтерес, є, звичайно, ті, в яких відбувається розрив зв’язку вуглець-сірка. У різних нафтових фракціях присутні кілька типів сполук сірки, таких як сульфіди, полісульфіди, меркаптани, тіофени, бензтіофени і дібензтіофени. Останні два типи з'єднань сірки переважають у більшості прямогонний газойлів та газойлів крекінгу. У процесі гідрознесірчення протікають такі реакції:
Гідрознесірчення: Бензотіофени Гідрознесірчення: Дібензотіофени Гідрознесірчення: Сульфіди
R1 — S — R2 + 2H2 > R1 H + R2 H + H2S
Гідрознесірчення: Меркаптани
R — SH + H2 > RH + H2S
Гідрознесірчення: Тіофен Реакції гідрознесірчення, для яких є термодинамічні дані, в цілому не обмежені рівновагою за будь-якої комбінації передбачуваних робочих умов, тобто при температурах від 200 до 500 °C і парціальному тиску водню до 300 бар абс. Проте глибока конверсія складних молекул, таких як 4,6-диметил дібензотіофен, добре протікає при високому парціальному тиску водню
При гідроочистці до дуже низького вмісту сірки потрібно також проводити конверсію більш стійких сполук сірки. Найбільш стійкими сполуками сірки є дібензотіофени більш високої молекулярної маси (тобто 4-метил дібензотіофен), що містять бічні ланцюги, які обмежують молекулі доступ до активних зон каталізатора. Ці більш стійкі сполуки присутні в більш високій концентрації в насиченому ароматики сировину, такому як каталітичні газойлі і продукти коксування.
Вуглеводні, що утворюються в результаті реакції гідрознесірчення, мають більш низьку температуру кипіння в порівнянні з вихідним з'єднанням сірки. У разі бензтіофена та відповідного етилбензолу різниця в температурі кипіння становить близько 80 є C. Може знадобитися або не знадобитися видаляти ці легкі вуглеводні з продукту, в залежності від типу, кількості і частки первинних з'єднань сірки, а також від специфікації на готовий продукт (наприклад щільність, температура спалаху)
2.2.2 Гідрогеноліз сполук азоту
За останнє десятиліття стало очевидно, що сліди азоту, дуже часто в поєднанні з певними сполуками сірки і кисню, можуть зробити істотний вплив на різні експлуатаційні характеристики нафтопродуктів. У порівнянні зі сполуками сірки, сполуки азоту присутні в нафті у відносно невеликій кількості.
Багато видів азотистих сполук були виявлені в нафтах, як з групи азотистих основ, наприклад, піридини, хіноліни, ізохінолін, бензохіноліни, так і з групи неосновних азотистих сполук, наприклад, пірол, індол, карбазол. У прямогінних фракціях були виявлені в невеликих кількостях ароматичних речовин або аліфатичні аміни. Більш того, сполуки азоту-сірки були виявлені в нафтах, в яких атоми азоту і сірки присутні в окремих кільцях молекули.
Як правило, чим вище температура кипіння нафти, тим вищий вміст азотистих сполук.
Рівноважні положення різних реакцій гідродеазотування точно не відомі. Наявні термодинамічні дані вказують на те, що, принаймні, для деяких сполук азоту і в температурному діапазоні 300−500 є C для протікання реакції гідродеазотування потрібна високий парціальний тиск водню.
Гідродеазотування:
CxHyNz + nH2 —-> zNH3 + CxHm
Для майже повного видалення азоту, в цілому, необхідно підняти
тиск / температуру вище діапазону, який застосовувався в минулому для знесірчення. Однак для глибокої сіркоочистки потрібно видалити і ці азоторганічні з'єднання, оскільки вони знижують активність каталізатора. Тому глибока сіркоочистки вимагає досить жорстких робочих умов, а саме парціального тиску водню, у порівнянні з минулим.
2.2.3 Гідрогеноліз сполук кисню
Сполуки кисню в різних фракціях, в цілому, досить легко піддаються гідрогенізації, якщо робочі умови досить жорсткі (температура, парціальний тиск водню). Зазвичай вміст кисню в нафті низька. Найбільш відомими сполуками кисню, присутніми в нафтах, є нафтенові кислоти та феноли.
Гідродезоксигенування:
CxHyOz + nH2 —-> zH2O + CxHm
Приклад: Фенол
2.2.4 Гідрування ароматичних та поліароматичних вуглеводнів
Значна кількість атомів вуглецю в молекулах нафтових фракцій присутній у вигляді кільцевих структур. Там присутні циклопентан, циклогексан, бензоли і конденсовані кільцеві структури (від повністю насичених сполук — полінафтенів — до сполук, які мають повністю ароматичну природу, — поліароматики).
Можуть протікати наступні реакції :
Гідрогенізація: бензолу Гідрогенізація: дібензотіофени
На підставі термодинамічних даних і з урахуванням температурного діапазону 300−500 °C і парціального тиску водню до 3МПа., Можна зробити наступні висновки:
1. Підвищення температури і зниження парціального тиску водню зміщують рівновагу в бік утворення ароматичних і поліароматичних вуглеводнів.
2. При незмінній температурі і парціальному тиску водню збільшення числа конденсованих кілець і збільшення числа алкільних ланцюгів на кожну поліароматичних молекулу веде до підвищення стабільності ароматичних вуглеводнів.
У залежності від каталізатора і вибраних робочих умов рівновагу насичення ароматики буде в більшій чи меншій мірі зміщуватися у бік повного насичення.
2.2.5 Гідрогенізація олефінів
У прямогінних нафтових фракціях присутні лише сліди олефінів. Оскільки в процесі насичення олефінів утворюється значна кількість теплоти, необхідно вжити особливих заходів обережності, переробляючи сировину з великим вмістом олефінів.
Можуть протікати наступні реакції гідрогенізації (насичення олефінів):
Насичення олефінів: моноолефіну Насичення олефінів: діолефіну Після чого На сучасних установках глибокого гідрознесірчення дизпалива при високому парціальному тиску водню ці реакції протікають дуже швидко і завершуються майже на 100%.
2.2.6 Гідрокрекінг
З точки зору термодинаміки, реакції гідрокрекінгу будуть протікати при будь-якому наборі передбачуваних умов реакції.
Таким чином, перебіг подібної реакції може бути обмежене лише за рахунок використання відповідного каталізатора і за рахунок підтримки температури реакції на як можна більш низькому рівні. На практиці, каталізатор і робочі умови підбирають таким чином, що гідрокрекінг на установці гідрознесірчення практично не спостерігається (не помітний у межах похибки експлуатаційних даних). Приклад реакції гідрокрекінгу — від'єднання етану:
Гідрокрекінг:
R1 — C — C — R2 + 2H2 > R1 + R2 H + CH3 — CH3
2.2.7 Конденсація ароматичних вуглеводнів
У даному контексті реакції конденсації - це ті реакції, в процесі яких відбувається утворення складних кільцевих структур з більш простих молекул (утворення «коксу» на каталізаторах). У цілому, природа сприяє утворенню молекул, бідних воднем, з конденсованими кільцями з більш простих молекул. У більшості випадків проміжними продуктами реакцій конденсації є поліароматичні вуглеводні з конденсованими кільцями. Більш високий парціальний тиск водню при незмінній температурі зменшить концентрацію подібних проміжних продуктів і, отже, утворення «коксу». Звідси тип утворених коксових / вуглецевих відкладень залежить від умов реакції. Спочатку виходить кокс полімерного типу, який при більш високих температурах перетворюється на кокс графітового типу. Плівка полімерного коксу і графітова плівка покривають поверхню металів каталізатора, позбавляючи каталізатор можливості виконувати свою конкретну задачу.
В умовах дегідрування при низькому парціальному тиску водню і високій температурі подальше підвищення температури сприяє утворенню вищевказаних проміжних продуктів і, отже, утворення «коксу». Підвищена концентрація в сировині молекул з конденсованими кільцевими системами також призведе до посиленого утворення «коксу» .
3. Характеристика сировини, реагентів, готової продукції
Таблиця 3.1 — Характеристика вихідної сировини, каталізаторів, продукції, що виготовляється[ 4 ]
Найменування сировини, матеріалів, реагентів, каталізаторів, продукції, що виготовляється | Показники якості, обов’язкові для перевірки | Норма | |
1. Фракція дизельного палива прямогонна | 1. Фракційний склад: — 10% переганяється при температурі, °С, не вище | Не нормується. Визначення обов’язково | |
СТП 02.06:2007 | — 50% переганяється при температурі, °С, не вище | ||
— 90% переганяється при температурі, °С, не вище | Не нормується Визначення обов’язково | ||
— 96% переганяється при температурі, °С, не вище | Не нормується Визначення обов’язково | ||
— температура кінця кипіння, °С | |||
— вихід % | Не нормується. Визначення обов’язково | ||
2. В’язкість кінематична при 20 °C, ммІ/с, в межах | 3,0 — 6,0 | ||
3. Температура спалаху, в закритому тигелі, °С, не нижче | |||
4. Густина при температурі 20 °C, кг/мі | Не нормується. Визначення обов’язково | ||
5. Масова частка сірки % | Не нормується. Визначення обов’язково | ||
6. Температура застигання, °С | Не нормується. Визначення обов’язково | ||
7. Випробування на мідній пластинці | Не нормується. Визначення обов’язково | ||
2. Воденьвмісний газ | 1. Об'ємна частка водню %, в межах. | 70−90 | |
СТП 02.101:2008 | 2. Об'ємна частка сірководня %, не більше | 0,003 | |
3. Масова частка вологи, що видаляється при 650 °C (ППП) %, не більше | 2,5 | ||
3. Каталізатор гідроочистки дизельних фракцій DC-2531 | 1. Насипна густина, кг/мі, не менше | ||
Фірма CriterionTM, Технологія acti CAT | 2.Розмір гранул, мм: ; діаметр довжина | 1,6 3−7 | |
4. Газ для технологічних печей | 1.Теплота згоряння кКал | Не нормується. | |
СТП 02.85:2008 | 2.масова часка сірководня не більше | 0,4 | |
5.Фракция дизельного палива гідроочищена | 1. Фракційний склад: — 50% переганяється при температурі, °С | ||
СТП 02.61:2009 | — 96% переганяється при температурі, °С температура кінця кипіння, °С — вихід, % | Не нормується. Визначення обов’язково | |
2. Масова частка сірки ррm, не більше | |||
3. В’язкість кінематична при 20 °C, ммІ/с, в межах | 3,0 -5- 6,0 | ||
4. Температура спалаху, в закритому тигелі, °С, не нижче | |||
5. Випробування на мідній пластинці | Витримує. Визначення обов’язково | ||
6. Густина при температурі 20 °C, кг/мі | Не нормується. Визначення обов’язково | ||
7. Температура застигання, °С | Не нормується. | ||
4. Вибір, обґрунтування та опис технологічної схеми
На основі розглянутого у розділі І та завданні до проектування береться установка Л-24−7. Каталізатором обрано кобальт-молібденовий каталізатор, розроблений фірмою CRITERIONtm — DC-2531, також у якості розподільчого пристрою в реакторі обрано розподільчу тарілку високої дисперсії розроблену фірмою SHELL
Установка Л-24−7[ 4 ] складається з двох рівнозначних потоків, на яких проводиться очищення прямогонної фракції дизельного палива або суміші прямогонної фракції дизельного палива з легким каталітичним газойлем (I і II потік) і прямогонної фракції палива для реактивних двигунів (II потік).
П — трубчаста піч; Р — реактор; Т — теплообмінники; Х — повітряний холодильник; С — сепаратори; Н — насос; 1 — сировина; 2 — воденьвмісний газ; 3 — свіжий воденьвмісний газ; 4 — вуглеводневий газ; 5 — дизельне паливо гідроочищене.
Рисунок 1.2- Технологічна схема установки Л24_7
Сировина поступає на прийом підпірного насоса Н-1 і при тиску не вище 0,6 МПа (6 кгс/смІ) через фільтри Ф-1, Ф-2, Ф-3 подається на прийом сировинного насоса Н2. Насосом Н-2 сировина з тиском до 5,2 МПа (52 кгс/смІ) подається в трійник змішення ТЗ куди компресором ПК-2 подається воденьвмісний газ.
Об'ємна частка водню в циркулюючому воденьвмісному газ, який подається в трійник змішення повинна бути не менше 70%.
Об'єм воденьвмісного газу на одиницю об'єму сировини в годину при мінімально допустимій об'ємній частці водню (70%), повинен складати не менше 250 нмі/год.
Газосировинна суміш після трійника змішення проходить міжтрубний простір сировинних теплообмінників Т-1,2,3 де нагрівається потоком газопродуктової суміші і поступає в колектор камери конвекції печі П-1. Для рівномірного розподілу газосировинної суміші на вході в піч П-1 по потоках встановлено 4 засувки. Під тиском не більше 5,2 МПа (52 кгс/смІ) з колектора газосировинна суміш чотирма потоками проходить послідовно змійовики конвекційної і радіантної камер і, об'єднавшись в один потік, з температурою 310−400 °С поступає в два послідовно працюючих реактора Р-1, Р-2.
Нагрівання газосировинної суміші в печі П-1 повинно здійснюватися з таким розрахунком, щоб температура димових газів на перевалі і після конвекційної частини не перевищувала 800 °C і 500 °C відповідно, при розрідженні після печі не більше 150 Па (15,0 кгс/мІ).
Об'ємна частка кисню в димових газах, що виходять з камери конвекції печі, повинна бути не більше 7%.
Паливний газ до форсунок печі П-1 подається з колектора паливного газу підприємства після відділення газового конденсату. Тиск в лінії паливного газу до печей повинен бути в межах 0,1−0,4 МПа (1,0 — 4,0 кгс/смІ).
Для підвищення безпеки ведення технологічного процесу на печі П-1 встановлені контрольні (пілотні) пальники.
Газосировинна суміш після печі П-1 поступає в реактори Р-1, Р-2, де на каталізаторі DC 2531 при тиску на вході в реактор Р-1 3,5−4 МПа (35,0−40,0 кгс/смІ) і при температурі 310−390 °С у присутності воденьвмісного газу відбуваються реакції процесу гідроочистки.
Температура зовнішніх стінок і штуцерів реакторів повинна підтримуватися в межах до 200 °C.
Газопродуктова суміш з реактора Р-2 поступає в трубний простір сировинних теплообмінників Т-1,2,3 де охолоджується газосировинною сумішшю, що проходить по міжтрубному простору.
Після сировинних теплообмінників газопродуктова суміш охолоджується в повітряному холодильнику Х-1 і з температурою не вище 50 °C поступає в сепаратор високого тиску С-1.
В сепараторі С-1 під тиском не більше 5,0 МПа (50 кгс/смІ) відбувається розділення газопродуктової суміші на водень, і нестабільний гідрогенізат.
Воденьвмісний газ змішується з свіжим воденьвмісним газом, який нагнітається компресором ПК-1 з колектора підприємства, і далі поступає на очищення від сірководня водним розчином моноетаноламіна (МЕА), масова частка МЕА в якому складає 5−15%.
Рідка фаза — нестабільний гідрогенізат — з сепаратора високого тиску С-1 надходить в сепаратор низького тиску С-2, де за рахунок зниження тиску до 0,8 МПа (8,0 кгс/смІ) від нього відділяється частина розчинених вуглеводневих газів і нестабільний гідрогенізат поступає на блок стабілізації.
5. Технологічні розрахунки
Вихідні данні до проекту:
Продуктивність установки по сировині т / рік — 6 000 000
Масова частка сірки в сировині % - 0,25
Меркаптанової - 0,1 225
Сульфідної - 0,1225
Дисульфідної - 0,0245
Тиофенової - 0,8 575
Масова частка ненасичених сполук в сировині% - 10
Склад свіжого ВСГ, об'ємні частки:
— Н2 — 85,02
— СН4 — 7.0
— С2Н — 6 — 5.08
— С3Н — 8 — 1.92
— С4Н — 10 — 0.98
Склад циркуляційного ВСГ, об'ємні частки:
— Н2 — 71.82
— СН4 — 19.64
— С2Н6 — 5.41
— С3Н8 — 1.94
— С4Н10 — 1.19
Кратність циркуляції ВСГ мі/мі - 250−400
Густина дизельного палива при 20Сє кг/мі - 850
Температура:
— на вході в реактор Сє - 350
— на виході з реактору С є - 358
Масова частка сірки в гідроочищеному ДП % - 0,005
5.1 Матеріальний баланс установки
5.1.1 Вихід гідроочищенного дизельного палива
Вихід гідроочищенного [ 7] дизельного палива ВД. П %(мас) на вихідну сировину дорівнює
ВД.П =100-Вб-Вг-ДS (5.1)
де Вб, Вг, ДS — виходи бензину, газу та кількість видаляємої сірки із сировини відповідно на сировину, %(мас).
Бензин та газ утворюються переважно при гідрогенолізу сірчистих сполук. При середньої молекулярної маси 209 в 100 кг сировини міститься 100:209=0,48 кмоль, 0,25 кг сірки містять 0,25:32=0,0078 кмоль сірки, тобто сірковмісні молекули складають 2% загального вмісту молекул. Якщо прийняти рівномірне розподілення атомів сірки уздовж вуглеводневої ланцюжки, то при гідрогенолізу сіркоорганічних сполук з розривом біля атому сірки з виходом бензину та газу складе Вб=ДS=0,245%(мас)