Проектування інструментальної оснастки деталі типу «Стакан»
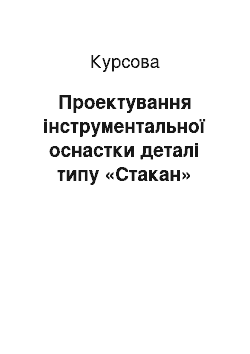
Переоцінка наявних методів проектування визвано такими чинниками, як комплексна механізація та автоматизація виробничих процесів, переоснащення машинобудівних підприємств сучасними металообробними верстатами та новим інструментом, модернізація ріжучого інструменту та нові матеріали його виготовлення, повсюдне впровадження в практику технології вибору інструментальної оснастки, електронних… Читати ще >
Проектування інструментальної оснастки деталі типу «Стакан» (реферат, курсова, диплом, контрольна)
Вступ
В процесі призначення стандартної та проектування нової інструментальної оснастки, виникає велика кількість проблемних питань які пов’язані із необхідністю виконання технічних вимог, що поставлені конструкторами перед виробництвом. Також ріжучий інструмент пов’язаний з експлуатацією складного обладнання металорізальних верстатів, тому етап вибору інструментальної оснастки дуже важливим та водночас трудомістким, адже від нього залежить якість деталей, які є основною продукцією машинобудівної галузі.
Переоцінка наявних методів проектування визвано такими чинниками, як комплексна механізація та автоматизація виробничих процесів, переоснащення машинобудівних підприємств сучасними металообробними верстатами та новим інструментом, модернізація ріжучого інструменту та нові матеріали його виготовлення, повсюдне впровадження в практику технології вибору інструментальної оснастки, електронних обчислювальних машин.
Отже, сучасне технологічне проектування це комплексна система взаємодії засобів і методів, що зумовлюють створення високоякісної технологічної документації на основі широкого використання стандартних технологічних вирішень.
Мета даного курсового проекту з різального інструменту, вибір та проектування інструментальної оснастки, деталі типу «Стакан» в умовах дрібносерійного виробництва.
Особливістю автоматизації в дрібносерійному виробництві є потреба у створенні гнучких виробничих систем, які здатні автоматично переходити з обробки деталей одного типорозміру на інший. У вирішенні цих задач провідну роль відіграють верстати з ЧПК та багатоцільові верстати. Адже використання одного такого верстата дозволяє замінити декілька фрезерних, свердлильних та розточних верстатів, при цьому значно підвищується продуктивність (в 2…3 рази) внаслідок скорочення допоміжного часу (в результаті автоматизації циклу обробки та автоматичної заміни інструменту).
В умовах реально діючих підприємств під час виготовлення деталей для зменшення можливого браку на окремих операціях можуть призначатися завищені значення припусків. В першу чергу це поясняється використанням застарілого обладнання. Наслідком цього є підвищення вартості заготовок, а також збільшення вартості механічної обробки.
Тому при виборі та проектуванні інструментальної оснастки в даному курсовому проекті була зроблена спроба використовувати оптимальний ріжучий інструмент та їхні характеристики. Рішення приймались з урахуванням рекомендацій ГОСТів.
Внаслідок виконання курсового проекту були отриманні практичні знання та навички, що потрібні не тільки при виконанні дипломного проекту, але і при роботі на виробництві.
1. Вибір стандартних різальних інструментів
1.1 Аналіз технологічності конструкції заданої деталі
Деталь стакан складовою частиною черв’ячного редуктора. Стакан з'єднаний з корпусом та використовується у якості корпусу для підшипників кочення у котрих насаджений вал черв’ячного колеса. Стакан має форму тіла обертання, але при цьому обертові рухи він не здійснює. Закріплюється стакан за допомогою отворів у фланці деталі. Поверхні посадок підшипників у стакан та поверхні посадки деталі стакан у корпус виконані з шорсткістю Rа 3,2 і мають призначений допуск співвісності. Ці поверхні повинні бути виконані відповідно до вимог креслення для забезпечення тривалого експлуатаційного терміну деталі. Стакан виготовлений зі Сталі 45, хімічний склад у таблиці 1.1.
Креслення деталі виконано на аркуші формату А2 за ГОСТ 2.104−68. Графи основного напису заповнені вірно і мають всі необхідні підписи. На кресленні зображено головний вид, головний вид у розрізі та вид зліва. На креслені проставлені всі необхідні розміри, квалітети точності та шорсткості. На креслені вказані такі технологічні вимоги: не вказані граничні відхилення розмірів за Н14, h14,, радіуси, що не вказані - 5 мм.
Таблиця 1.1. — Хімічний склад сталі 45 (ГОСТ 1050−74)
Елемент | Вміст, % | |
С | 0,42…0,5 | |
Si | 0,17…0,37 | |
Mn | 0,5…0,8 | |
S | до 0,04 | |
P | до 0,035 | |
Ni | до 0,3 | |
Cr | до 0,25 | |
Таблиця 1.2. — Механічні властивості стали 45
МПа | МПа | % | % | Дж/см2 | Твердість НВ | |
не менше | Не більше | |||||
1.2 Вибір обґрунтування послідовності обробки поверхонь деталі
Керуючись кінцевими вимогами до точності і якості поверхонь деталей вибираю поступово застосовувані технологічні методи обробки, сукупність яких забезпечить задану на робочому кресленні якість поверхні. Обрану послідовність обробки приводжу в таблиці 1.3.
Таблиця 1.3-Вибір і обґрунтування послідовності обробки
№ поверх. | Розмір, мм | Шорсткість, Ra | Квалітет | Допуск, мкм | Послідовність технологічних методів обробки | Примітка | |
Торець ? 410 | 6,3 | Підрізка торця | |||||
Торець ? 440 | 6,3 | Підрізка торця | |||||
? 335 L 685 | 12,5 | Розточування внутрішньої поверхні | |||||
? 440 L 35 | 12,5 | Точіння | |||||
Торець ? 560 | 12,5 | Підрізка торця | R2 | ||||
? 440 L 22 | 12,5 | Точіння | |||||
Торець ? 560 | 12,5 | Підрізка торця | |||||
? 420 L 100 | 12,5 | Точіння | |||||
? 440 L 83 | 12,5 | Точіння | |||||
? 345 | 12,5 | Розточування внутрішньої поверхні | |||||
? 360 L 145 | 3,2 | Розточування чорнове Розточування чистове | Розточування внутрішньої поверхні | ||||
? 370 L 40 | 12,5 | Точіння чорнове Точіння чистове | Точіння канавки | ||||
Фаска ? 360 3*45° | 12,5 | 14/2 | Розточування фаски | ||||
? 410 L 422 | 12,5 | Точіння | |||||
Фаска ? 440 3*45° | 12,5 | 14/2 | Зняття фаски | ||||
? 360 L 450,5 | 12,5 | Розточування внутрішньої поверхні | |||||
? 340 L 52 | 3,2 | Розточування внутрішньої поверхні | |||||
Фаска ? 340 3*45° | 12,5 | 14/2 | Розточування фаски | ||||
? 120 | 12,5 | Свердлення? 20, розсвердлення ?60, розточування | |||||
? 160 | 12,5 | Фрезерування торцю | |||||
L 96 | 12,5 | Фрезерування двох уступів | |||||
Отвір ? 6,7 | 12,5 | Свердління чотирьох отворів під різьбу | |||||
М8 | 6,3 | 7Н | Нарізання різьби | ||||
Отвір ? 10 | 12,5 | Свердління чотирьох отворів | |||||
? 17,3 L 35 | 12,5 | Свердління шести отворів | |||||
М20 L 25 | 6,3 | 7Н | Чорнове нарізання різьби | ||||
Чистове нарізання різьби | |||||||
Фаска М20 2*45° | 3,2 | 14/2 | Зенкування фаски | ||||
Отвір ? 20,7 | 12,5 | Свердління чотирьох отворів | |||||
М24 | 6,3 | 7Н | Чорнове нарізання різьби | ||||
Чистове нарізання різьби | |||||||
Отвір ? 13,8 L 35 | 12,5 | Свердління шести отворів | |||||
М16 L 25 | 6,3 | 7Н | Чорнове нарізання різьби | ||||
Чистове нарізання різьби | |||||||
Фаска М16 2,5*45° | 6,3 | 14/2 | Зенкування фаски | ||||
Отвір ? 26 | 12,5 | Свердління восьми отворів | |||||
1.3 Вибір металорізальних верстатів та інструментів для обробки поверхонь деталі
З урахуванням кількості і змісту раніше передбачених технологічних методів обробки поверхонь, необхідно вибрати тип металорізального обладнання та інструментів. Дані заносимо до таблиці 1.4.
Таблиця 1.4 — Вибір металорізальних верстатів та інструментів
№ поверхні | Найменування операції | Тип і модель верстату | Тип інструменту | Примітки | |
1, 2 | Підрізка торця | Токарно-гвинторізний 16К50 | Ріцезь підрізний, прохідний відігнутий з напаяною пластиною із твердого сплаву | ||
12, 17, 18 | Точіння | Токарно-гвинторізний 16К50 | Ріцезь підрізний, прохідний відігнутий з напаяною пластиною із твердого сплаву | ||
4, 5, 6, 7, 8, 9, 12, 14 | Точіння чистове | Токарно-гвинторізний 16К50 | Різець чистовий широкий з пластиною із твердого сплаву | ||
3, 10, 11, 16, 18 | Розточування внутрішньої поверхні | Токарно-гвинторізний 16К50 | Різець розточний для обробки наскрізних отворів | ||
20, 23, 25, 26, 29, 31, 34 | Свердління отворів | 2А587 | Свердло спіральне | ||
24, 27, 30, 32 | Нарізання різьби | 2А587 | Мітчики машинні - ручні | ||
23, 28 | Зенкування фаски | 2А587 | Зенківка конічна | ||
Фрезерування торцю | 2А620Ф2 | Фреза торцева насадна з вставними ножами із швидкоріжучої сталі | |||
Фрезерування уступа | 2А620Ф2 | Фреза шпонкова | |||
1.4 Вибір параметрів різальної частини інструментів
З урахуванням фізико — механічних параметрів матеріалу деталі, виду обробки і використаних металорізальних верстатів для прийнятих металорізальних інструментів призначити матеріали різальної частини, вибрати геометричні параметри і параметри з'єднувальної частини. Дані фіксую у таблиці 1.5.
Таблиця 1.5 — Вибір параметрів різальної частини інструментів
№ поверхні | Тип інструменту | Матеріал різальної частини інструменту | Матеріал державки (корпуса, хвостовика інструмента | Геометричні параметри ріжучої частини | |
1, 2, 12, 17, 18 | Різець підрізний відігнутий з напаяною пластиною із твердого сплаву | Т5K10 | Сталь 50 | ;;; | |
4, 5, 6, 7, 8, 9, 12, 14 | Різець чистовий широкий з пластиною із твердого сплаву | Т15К6 | Сталь 50 | ;;; | |
3, 10, 11, 16, 18 | Різець розточний для обробки наскрізних отворів | Т15К6 | Сталь 50 | ;;; | |
20, 23, 25, 26, 29, 31, 34 | Свердло спіральне з конічним хвостовиком | Р6М5 | Сталь 45 | ||
24, 27, 30, 32 | Мітчики машинні - ручні | Р18 | Сталь 45 | ||
23, 28 | Зенківка конічна | Р18 | Сталь 45 | ||
Фреза торцева насадна з вставними ножами із швидкоріжучої сталі | Р18 | Сталь 40ХН | ц = 10°; ц1 = 7° б = 5°; r = 0,4 мм | ||
Фреза шпонкова | Р18 | Сталь 40 | ц1 = 5°; г = 5°; б = 12°; r = 0,2 мм | ||
1.5 Розрахунок конструктивних параметрів різального інструменту
Для одного з прийнятих типів інструментів вибираються найбільш навантажені умови роботи (чорнова обробка). З урахуванням умов різання (фізико-механічні властивості матеріалу деталі, характеристики верстата, і режимів різання) укрупнено визначаються сили різання. Прийнятий інструмент перевіряється на твердість і міцність для найбільш навантажених умов обробки.
різець — розрахунок державки на міцність та твердість осьовий інструмент — розрахунок на міцність під дією обертового моменту і зусилля подачі.
фреза — розрахунок оправки на міцність під дією сумарного зусилля подачі;
протяжка — розрахунок на міцність під дією сумарного зусилля;
1.5.1 Розрахунок державки різця на твердість та міцність
Розрахунок державки різця підрізний відігнутий з напаяною пластиною із твердого сплаву на міцність та твердість ТУ 2−035−892−82 для чорнового обточування зовнішньої поверхні деталі стакан зі сталі 45 з =750 МПа (?75кгс/мм).
Найбільший діаметр деталі D = 560 мм, глибина точіння t = 3 мм, подача на оберт =0,3мм/об, виліт різця l = 70 мм, швидкість головного руху різання 110м/хв.
а) В якості матеріалу для корпуса різця обираю сталь 50 з =650 МПа (?65кгс/мм) Та допустимим напруженням на згин = 200МПа (?20кгс/мм) б) Головна складова сили різання
==1983 Н (?198 кгс) Значення коефіцієнтів та показників степені формул для, зовнішнього прокольного точіння сталі з границею міцності =750 МПа різцем з пластиною з твердого сплаву:
= 300; х = 1; у= 0,75;
— сумарний поправочний коефіцієнт;
в) При умові, що h =1,6b, ширина прямокутного перерізу різця дорівнюватиме:
=
або в одиницях СІ
=
Приймаємо найближчий більший переріз корпусу (b=12мм). Керуючись приведеними співвідношеннями, отримуємо висоту різця h=1,6b=
Приймаємо h = 20 мм. За ТУ 2−035−892−82 приймаємо параметри b? h =12?20.
г) Перевіряємо міцність та жорсткість корпусу різця:
Максимальне навантаження, допустиме міцністю різця:
в одиницях СІ
(?229 кгс) Максимальне навантаження, що допускається жорсткістю різця;
кгс в одиницях СІ
(?456 кгс),
де f=0,1(?0,1мм) — допустима стріла прогину різця при чорновому точінні;
Е=2 МПа=2= 20 000 кгс/мм — модуль пружності матеріалу корпусу різця;
l=70 мм — виліт різця;
J — момент інерції прямокутного перерізу корпусу;
в одиницях СІ
Різець має достатню міцність та жорсткість, так як
1.6 Вибір типорозміру різальних інструментів
З урахуванням виду обробки, типу інструменту, параметрів різальної частини, і габаритів, визначених за умовою міцності, призначаються типорозміри стандартних металорізальних інструментів. Дані занести в таблицю 1.6.
Таблиця 1.6 — Вибір типорозмірів інструментів
№ поверхні | Найменування інструмента | Основні розміри інструмента, мм | Матеріал різальної частини | Шифр інструмента ГОСТ | |
1, 2, 12, 17, 18 | Різець підрізний відігнутий з напаяною пластиною із твердого сплаву | H=25; В=25; L=170; H=32; В=20; L=170; H=25; В=25; L=170; | Т5K10 | 2102−1117 ГОСТ 18 877– — 73 2112−0063 ГОСТ 18 880– — 73 2103−1131 ГОСТ 18 879– — 73 | |
4, 5, 6, 7, 8, 9, 12, 14 | Різець чистовий широкий з пластиною із твердого сплаву | H=25; В=25; L=140; | Т15К6 | 2120−0052 ГОСТ 18 881- 73 | |
3, 10, 11, 16, 18 | Різець розточний для обробки наскрізних отворів | H = 25; В = 25; L = 170; | Т15К6 | 2140−0045 ГОСТ 18 877 — 73 | |
20, 23, 25, 26, 29, 31, 34 | Свердло спіральне з конічним хвостовиком | ?20 L120; ?60 L250; ?6,7 L65; ?10 L120; ?20,7 L200; ?13,8 L150; ?26 L170; ?8 L100 | Р6М5 | ГОСТ 10 903 — 77 | |
24, 27, 30, 32 | Мітчики машинні - ручні | М8; М16; М20; М24; | Р12 | ГОСТ 3266–81 | |
23, 28 | Зенківка конічна | ?16; б=90°; щ=15° | Р18 | 2353 — 0104 ГОСТ 14 953–80 | |
Фреза торцева насадна з вставними ножами із швидкоріжучої сталі | D=160 мм; В=45 мм; d = 50 мм; z = 16 | Р18 | ГОСТ 1092–80 | ||
Фреза шпонкова | d = 10; L = 63 мм; l = 13 мм | Р18 | 2234−0365 ГОСТ 9140–78 | ||
2. Проектування спеціального інструмента
На основі аналізу методів обробки поверхонь та вибраних типів ріжучих інструментів виконуємо розрахунок спеціального ріжучого інструмента — різця фасонного.
Вихідні дані до розрахунку:
— Ескіз операції для якої здійснюється розрахунок спеціального ріжучого інструменту, що зображений на рисунку 2.1;
— Тип і модель верстату;
— Посадочне місце шпинделя верстата;
— Матеріал деталі та визначення границі міцності.
Рисунок 2.1 — Ескіз операції
В якості матеріалу для корпуса різця обираємо вуглецеву Сталь 45 ГОСТ 1050–88 з = 610 МПа та допустиме навантаження на згин = 200 МПа. Головна складова сили різання обчислюється за формулою (2.1).
(2.1)
При умові, що, ширина прямокутного перерізу корпусу різця обчислюється за формулою (2.2).
(2.2)
м =11 мм Приймаємо найблищий більший переріз корпуса (b=20 мм), враховуючи посадочне місце під різець даного станка. Користуючись приведеними співвідношеннями, отримуємо висоту різця h=25 мм.
Перевіряємо міцність та жорсткість корпусу різця.
Максимальне навантаження, що допускається міцністю різця:
Максимальне навантаження, що визначається жорсткістю різця де J - момент інерції перерізу різця, що обчислюється за формулою м4
Отже, обраний переріз різця задовольняє всі умовам міцності та жорсткості.
Вибір матеріалу ріжучої частини Обираємо матеріал ріжучої пластини Т5К10 ГОСТ 3882–74 та пластину 0046 ГОСТ 25 395–82.
У технічних вимогах вказуємо матеріал ріжучої пластини, вид пластини, матеріал державки. Невказані граничні відхилення становлять h14, IT14/2. Матеріал припою — латунь Л68 або іншої марки по ГОСТ 15 527–70, розрив слою припою не повинен перевищувати 0,1 мм, розрив слою припою не повинен перевищувати 15% його загальної довжини. Маркувати — КТУ.7 090 202.Т5К10.
3. Розробка інструментального налагодження
Інструментальне налагодження представляє комплекс ріжучих і допоміжних інструментів, скомпонованих відповідно до конструкції деталі і змісту технологічної операції. Інструментальний комплекс складається послідовно від основного ріжучого інструмента, через набір допоміжних інструментів до посадкових поверхонь металорізального верстату (шпиндель). При проектуванні налагодження враховуються тип виробництва, точність, продуктивність і зручність обслуговування інструментального комплексу. деталь різець інструмент поверхня На рисунку 3.1зображений ескіз операції, для якої виконується налагоджування горизонтально — розточного верстату моделі 2А 587.
Розробку інструментального налагодження проводимо на операцію нарізання метричної різьби М20. Операцію проводимо на радіально-свердлильному верстаті моделі 2А587 схема якого зображена на рисунку 3.2 та основні технічні дані у таблиці 3.2. Ескізи шпинделя та столу верстата зображені на рисунках 3.3 та 3.4 відповідно. Для здійснення цієї операції використовуємо мітчик. Вибір допоміжних інструментів здійснюємо приймаючи до уваги посадочне місце шпинделя верстата, що представлене конусом Морзе № 1 та зображеному на рисунку 3.2, та посадочні параметри інструмету. Таким чином, по посадочним розмірам мітчика обираємо втулку перехідну швидкозмінну для мітчиків. По розмірам обраної втулки обираємо патрон для швидкозмінного інструмета. Вибранні допоміжні інструменти заносимо до таблиці 3.1.
3.1 Вибір допоміжних інструментів
З урахуванням параметрів оброблюваної поверхні, способу базування деталі, типу верстату й основних розмірів прийнятого стандартного ріжучого інструмента, вибираємо допоміжний інструмент із вказанням його конструктивних параметрів. Дані зводимо в таблицю 3.1.
Таблиця 3.1 — Вибір допоміжного інструменту для радіально — свердлильного верстату моделі 2А 587.
Різальний інструмент | Допоміжний інструмент | |
Свердло спіральне 2301−3656 ГОСТ 10 903- 77, d = 17,3 мм, L=140мм, l =165 мм, конус Морзе № 3 | Втулка 6100−0143 ГОСТ 13 598–85, D=12,825 мм, L = 112 мм, a=18,0 мм | |
Мітчик М20×2,5 2621−1731 ГОСТ 3266–81 | Втулка перехідна швидкозмінна жорстка для мітчиків 6143−0114 ГОСТ 15 936–70 | |
Зенківка 2353 — 0104 ГОСТ 14 953–80, D=16 мм, d = 10 мм, L=116 мм, l = 24 мм, конус Морзе № 2 | Втулка 6100−0143 ГОСТ 13 598–85, D=12,825 мм, L = 112 мм, a=18,0 мм | |
Рисунок 3.1 — Ескіз операції
Рисунок 3.3 — Ескіз шпинделя верстата 2А587
Рисунок 3.4 — Ескіз столу верстата 2А587
Література
1. Металлорежущие станки: номенклатурный каталог. В 2-х ч. — М: ЦНИИмаш. 1989…1993.
2. Кузнецов Ю. И., Маслов А. Р., Байков А. Н. Оснастка для станков с ЧПУ: Справочник. — М.: Машиностроение, 1983.-352с
3. Обработка металлов резанием: Справочник технолога. / Под общ. ред. Панова А. А. — М.: Машиностроение, 1988. — 736с.
4. Справочник инструментальщика. /Под ред. Ординарцев И. А. — Л.: Машиностроение Ленинград. отделение, 1987. — 846с.
5. Инструмент для металлообрабатывающих станков. Основные размеры и рекомендации по применению ч. 1 — Вып. 3, ч. 4. М., НИИинформации по машиностроению, 1968., ч. 1. Вып. 3. Режущий инструмент: сверла, зенкеры и развертки. Справочник для машиностроителя. (Изд. перераб. и доп.) 416с. ч. 4. Вспомогательный инструмент (Второе издание испр. и доп.) 502с.
6. Справочник технолога-машиностроителя. /Под ред. Косиловой А. Г. и Мещерякова Р. К. — М.: Машиностроение, 1985. Т.1, Т.2.
7. Нефедов Н. А., Осипов К. А. Сборник задач и примеров по резанию металлов и режущему инструменту: Учебное пособие — М.: Машиностроение, 1990. — 448с.
8. Резцы с твёрдосплавными пластинами ГОСТ 5688–61
9. Свёрла спиральные ГОСТ 12 121–77
10. Свёрла спиральные. Технические условия. ГОСТ 2034;80.
11. Зенкеры ГОСТ 14 953–80
12. Фрезы концевые ГОСТ 9140–78
13. Метчики машинно-ручные ГОСТ 3266–81
14. Серебряницкий П. П. Вспомогательный инструмент для металлорежущих станков. — Лениздат, 1974.